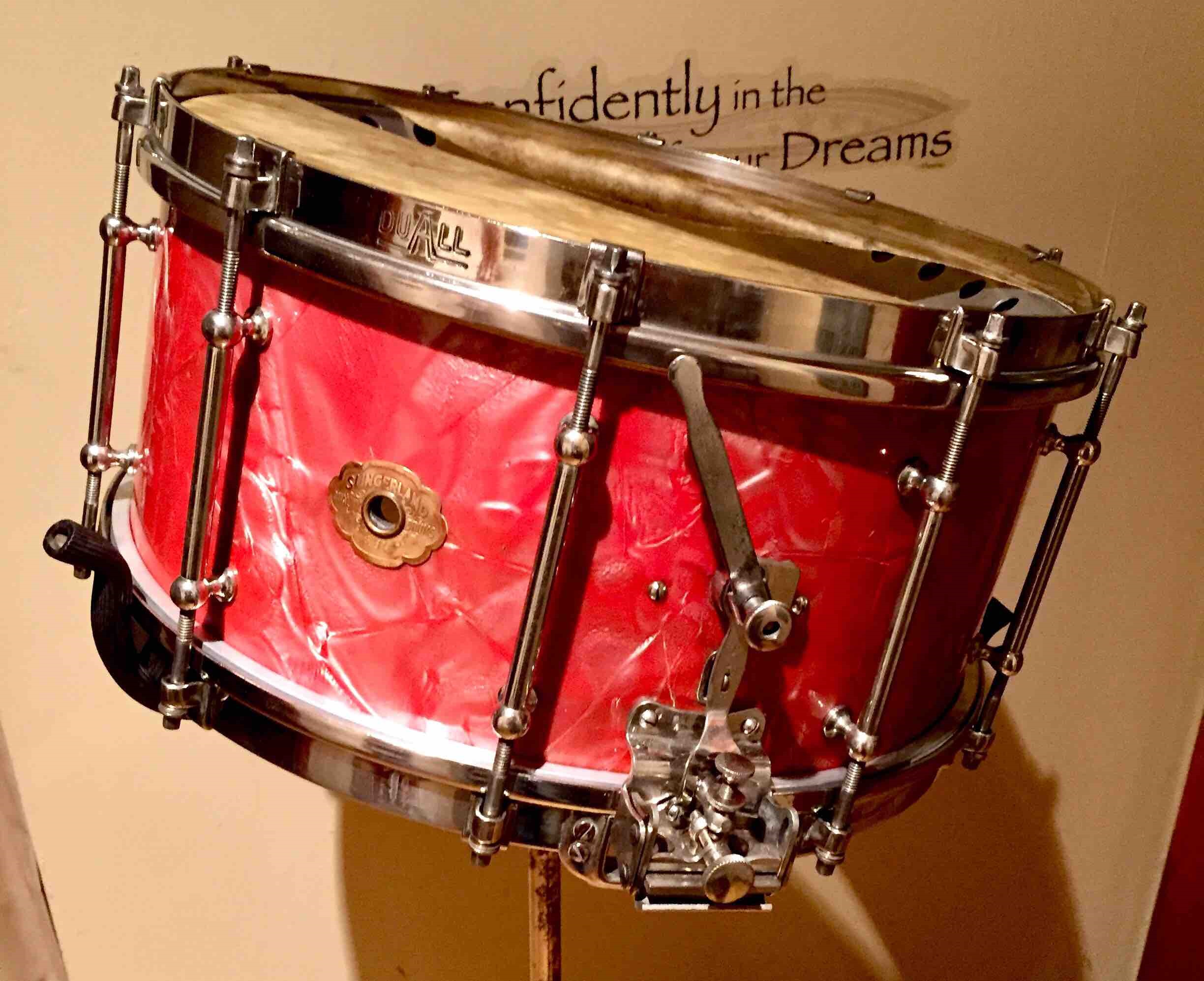
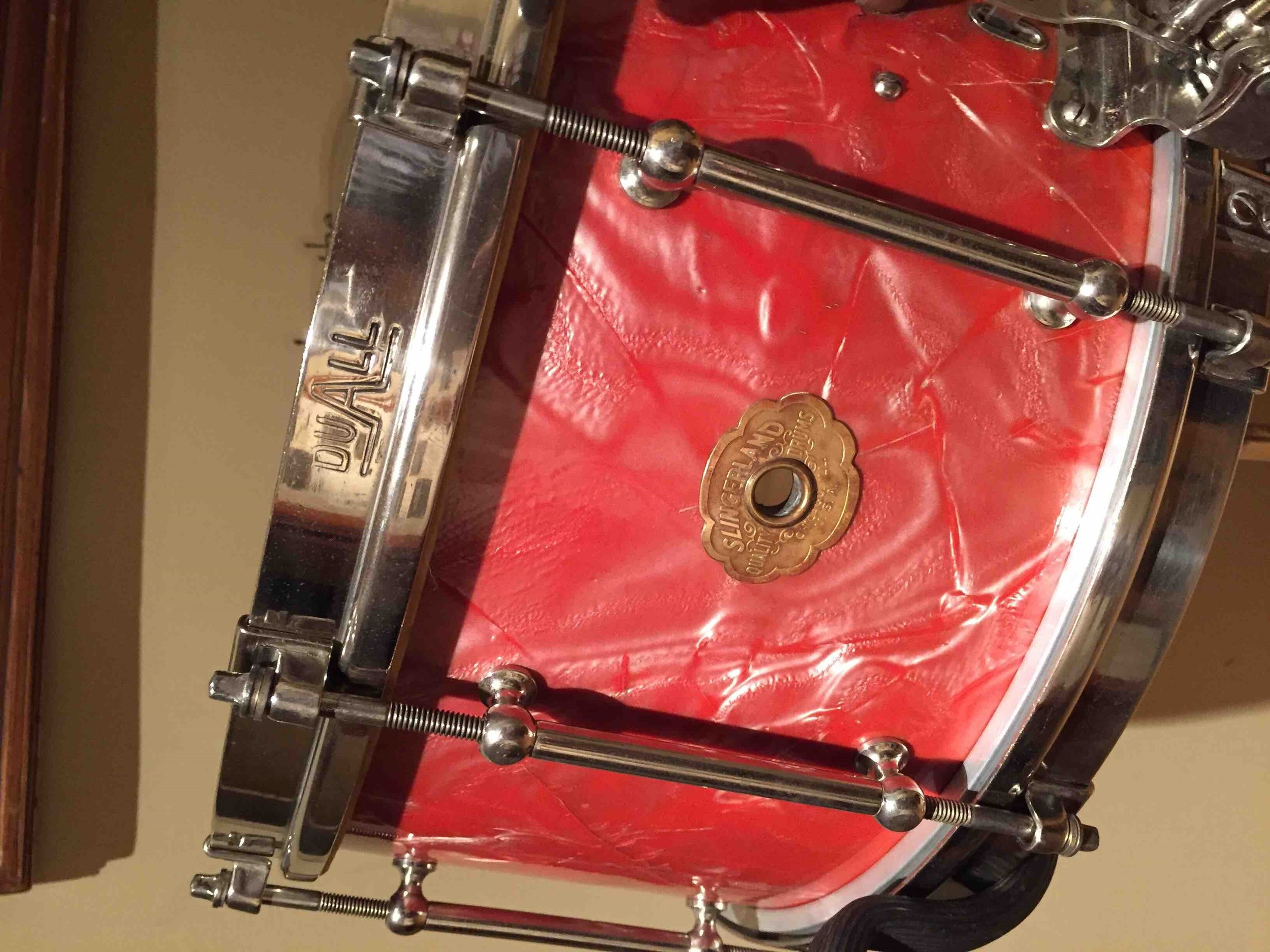

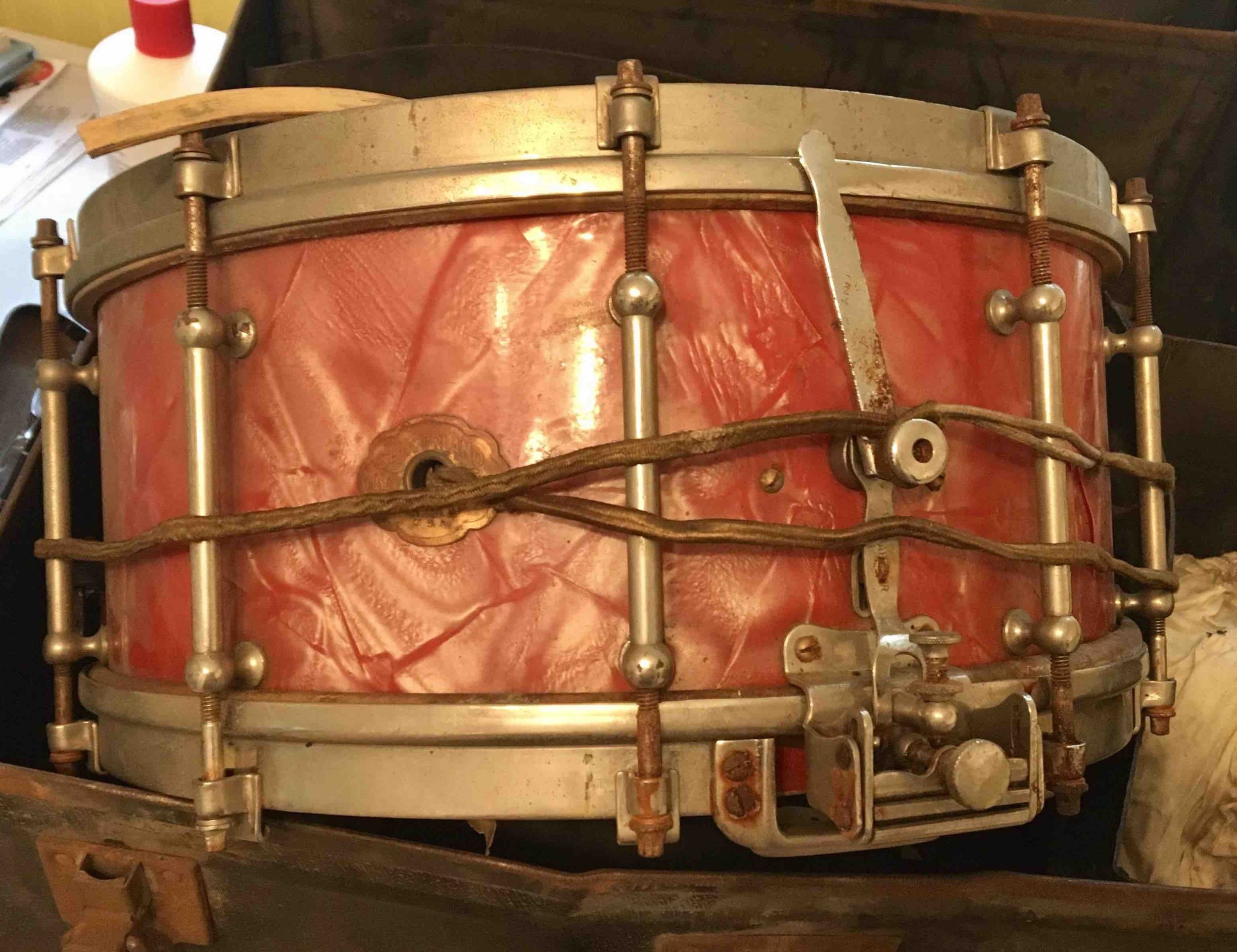
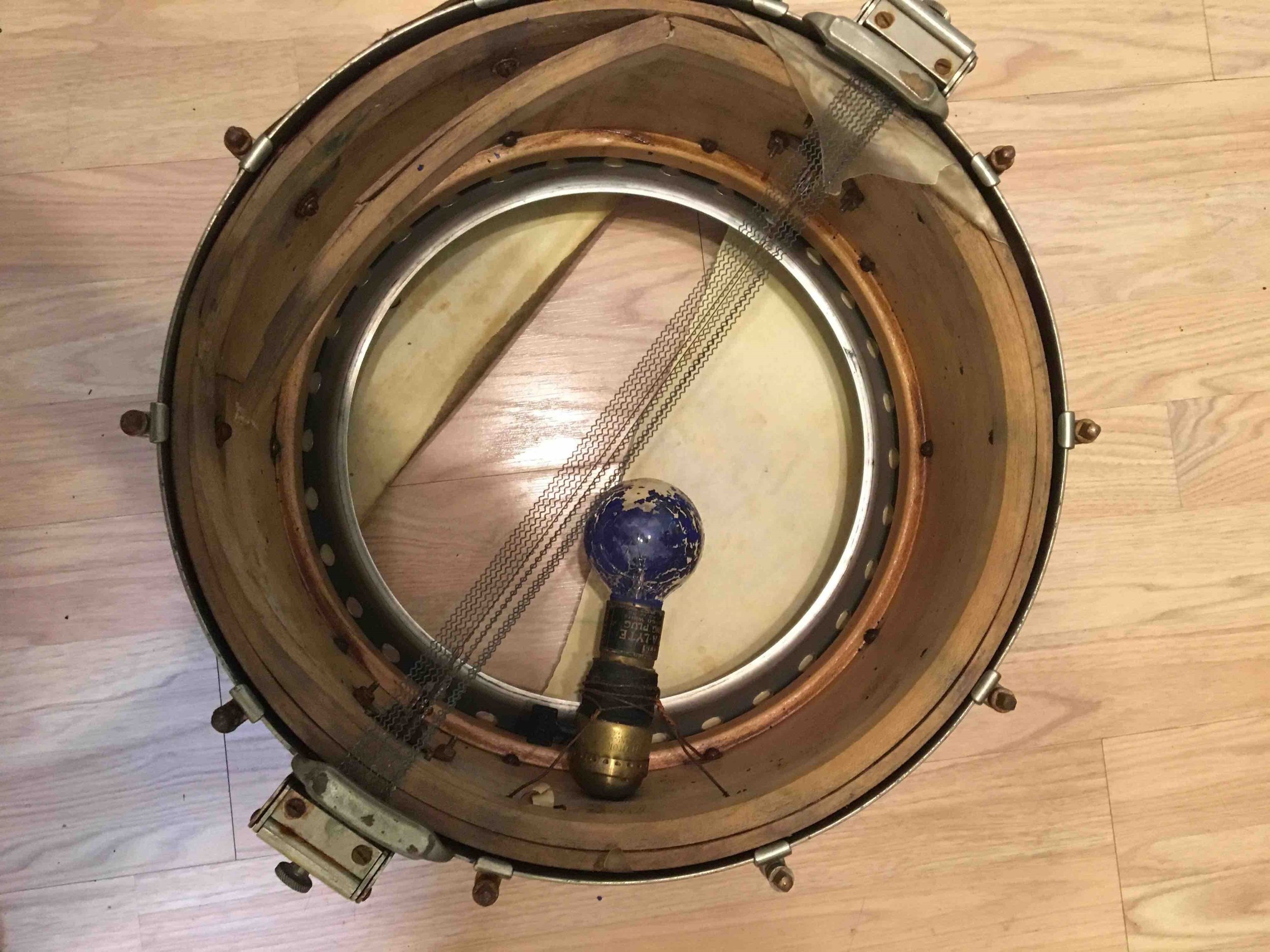
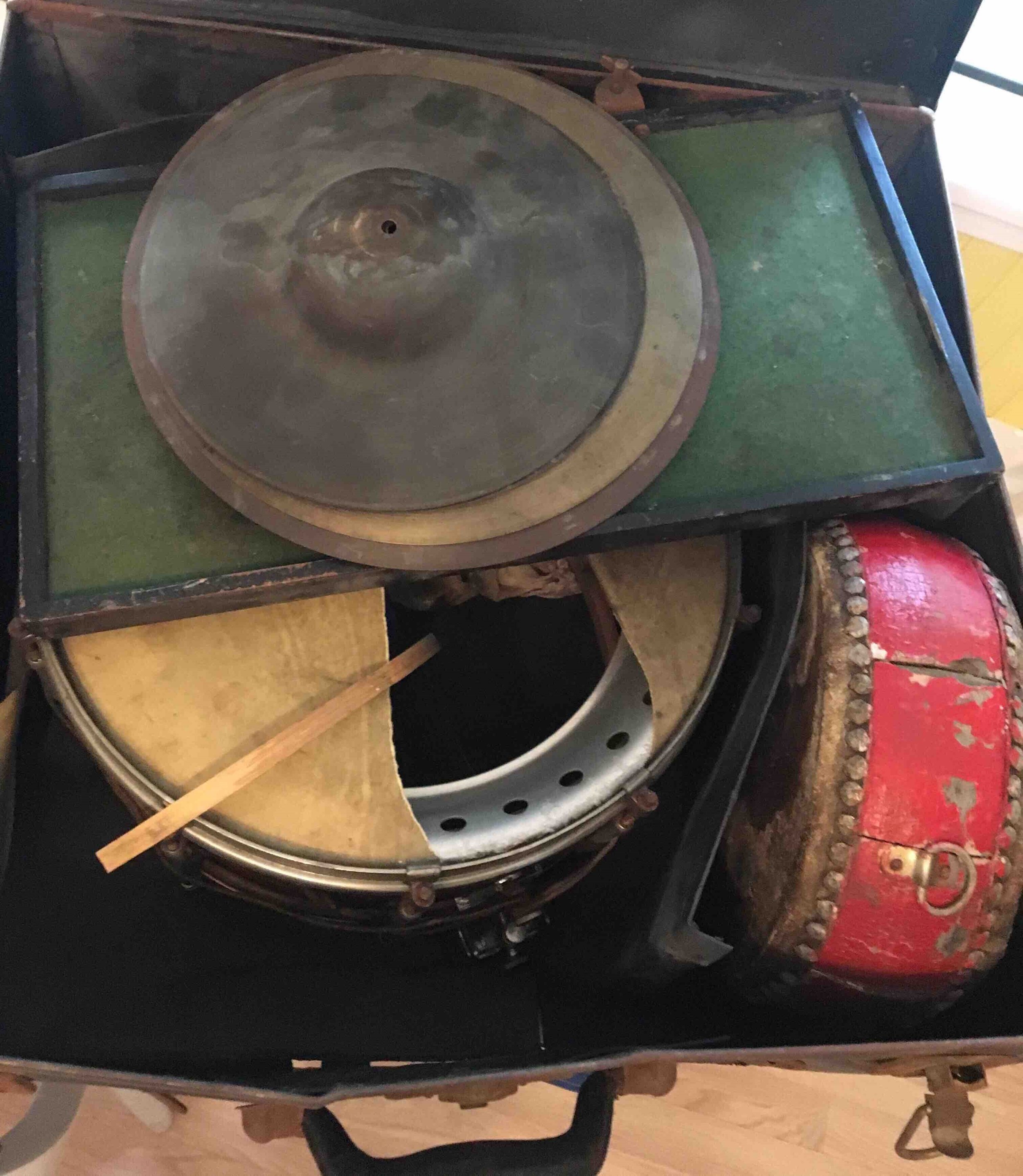
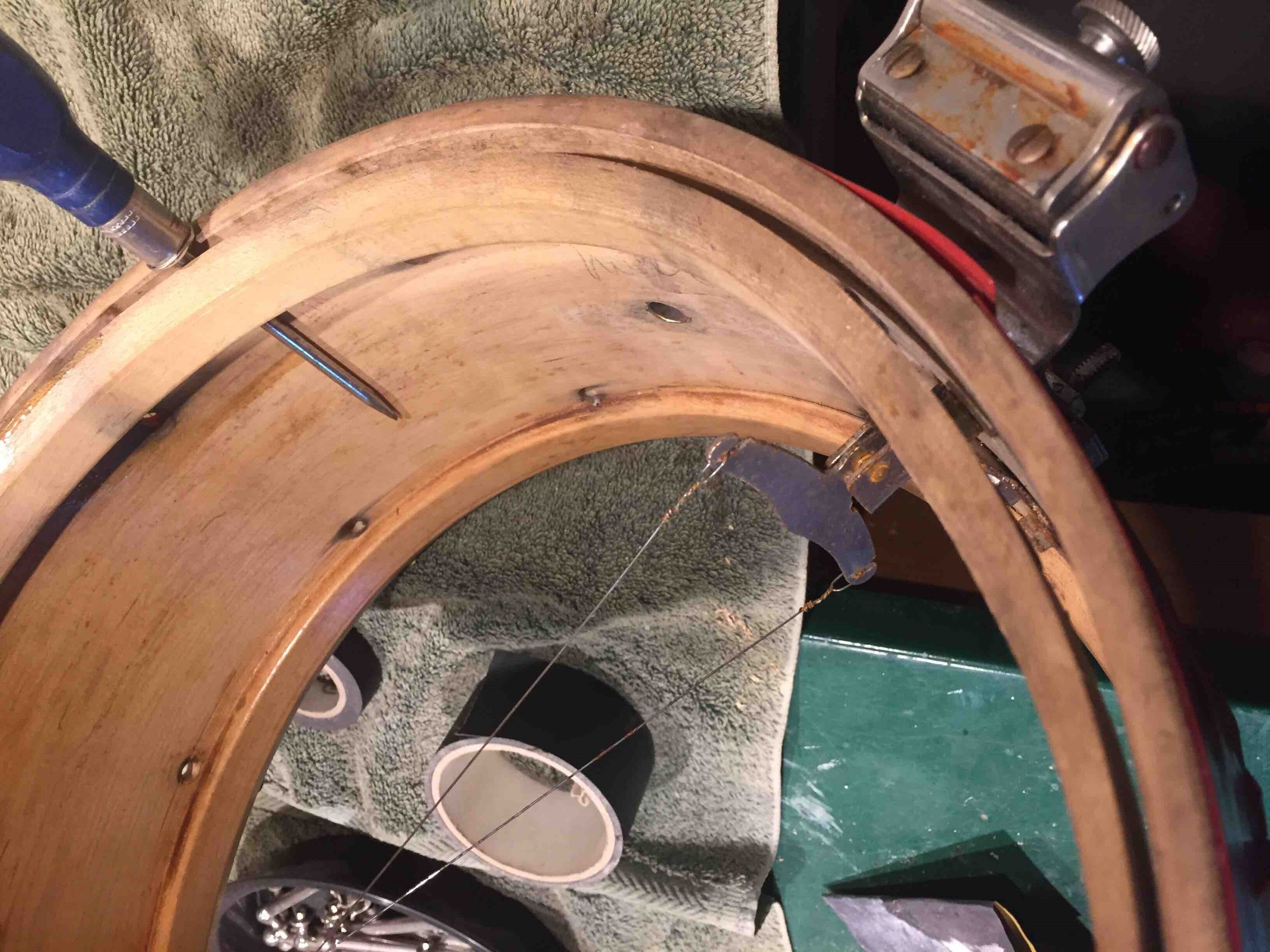
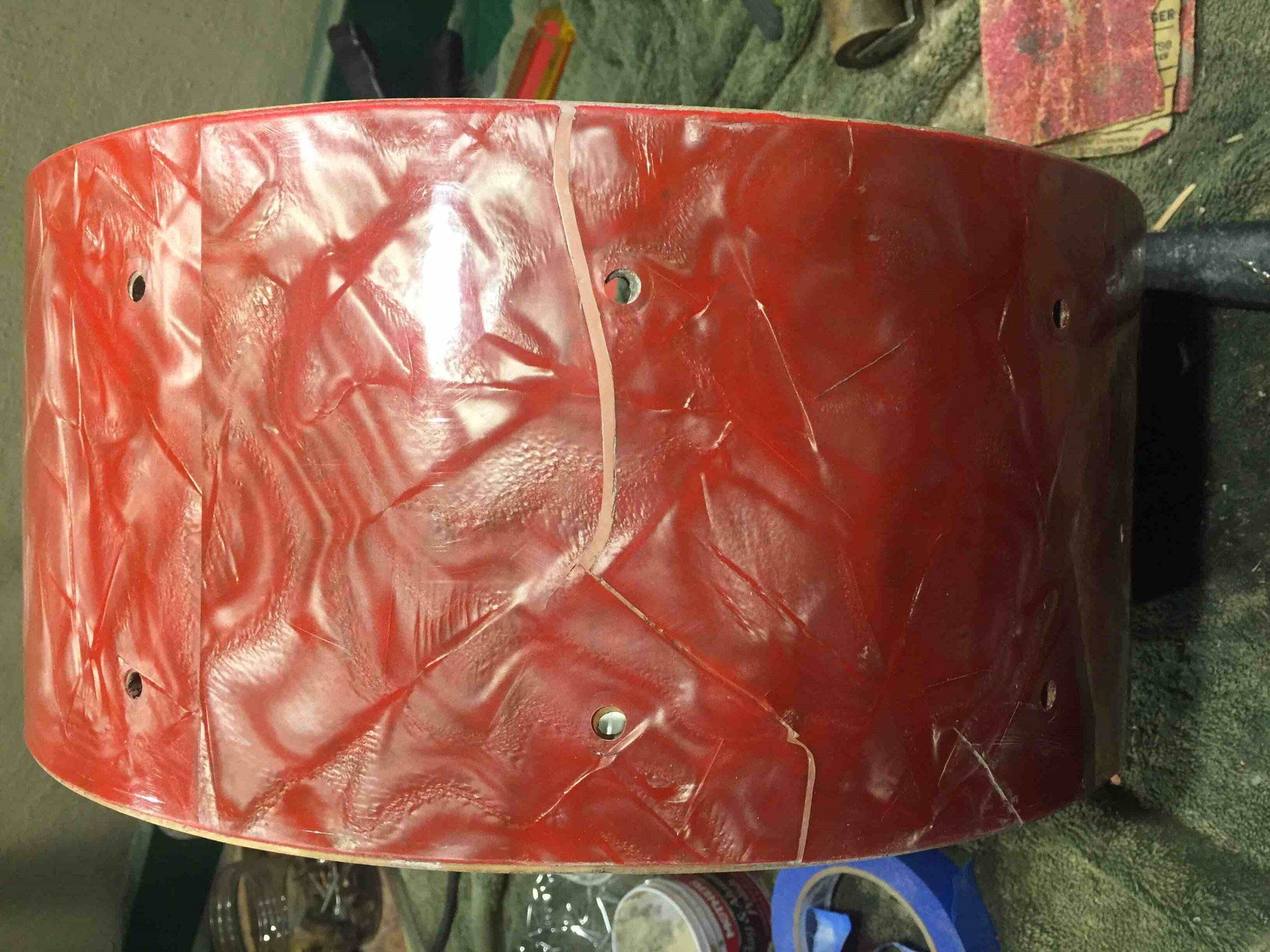
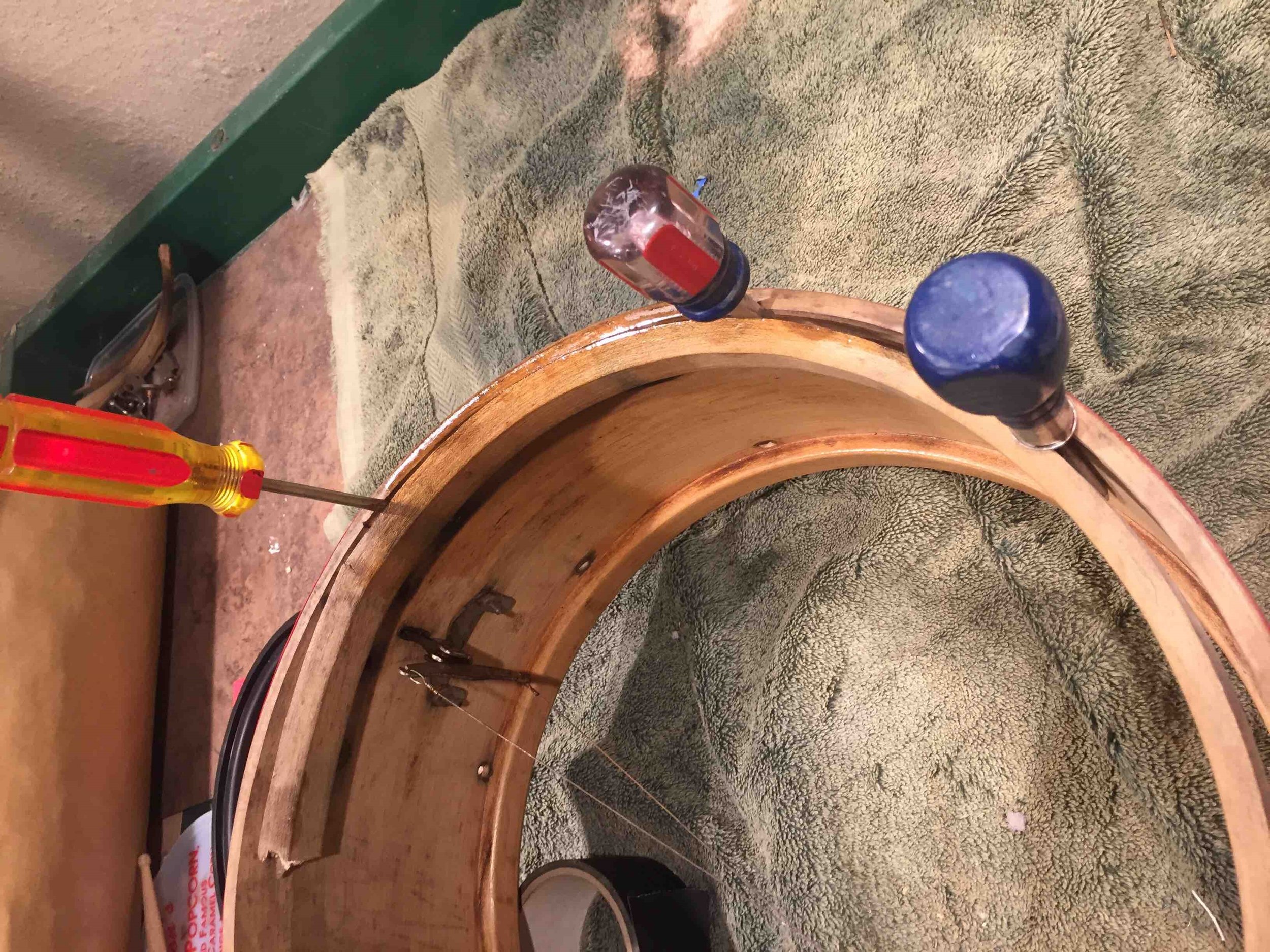
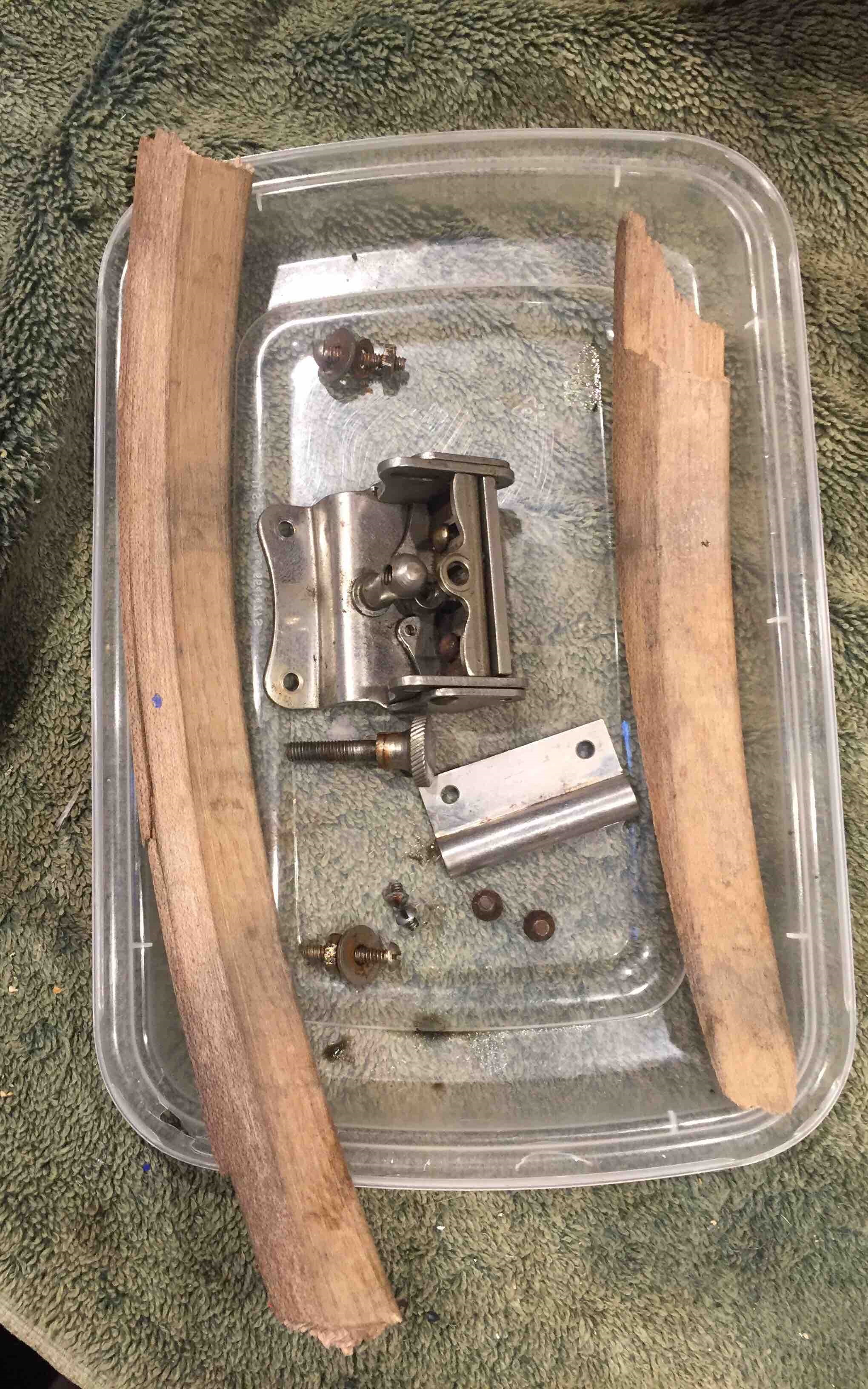
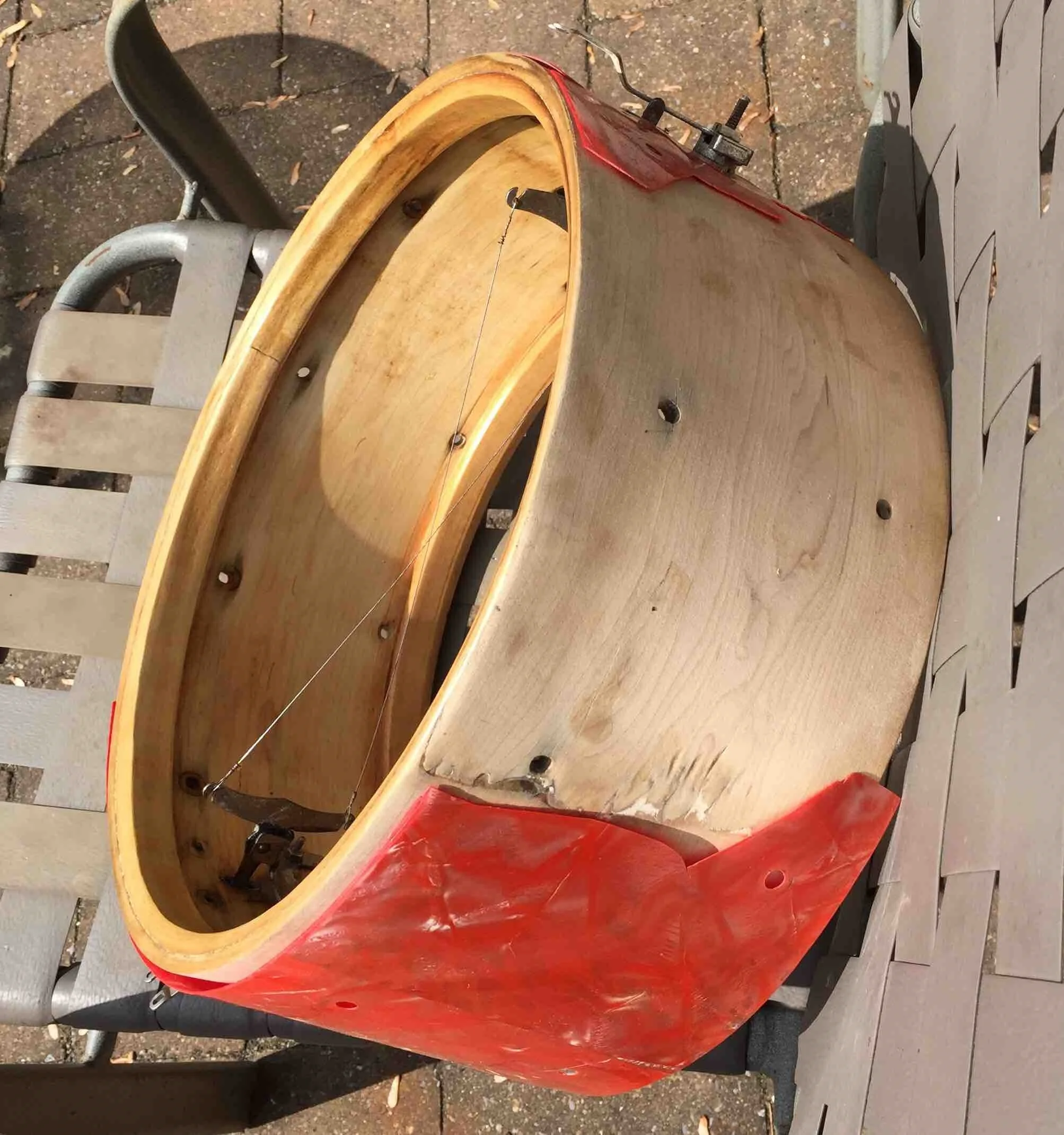
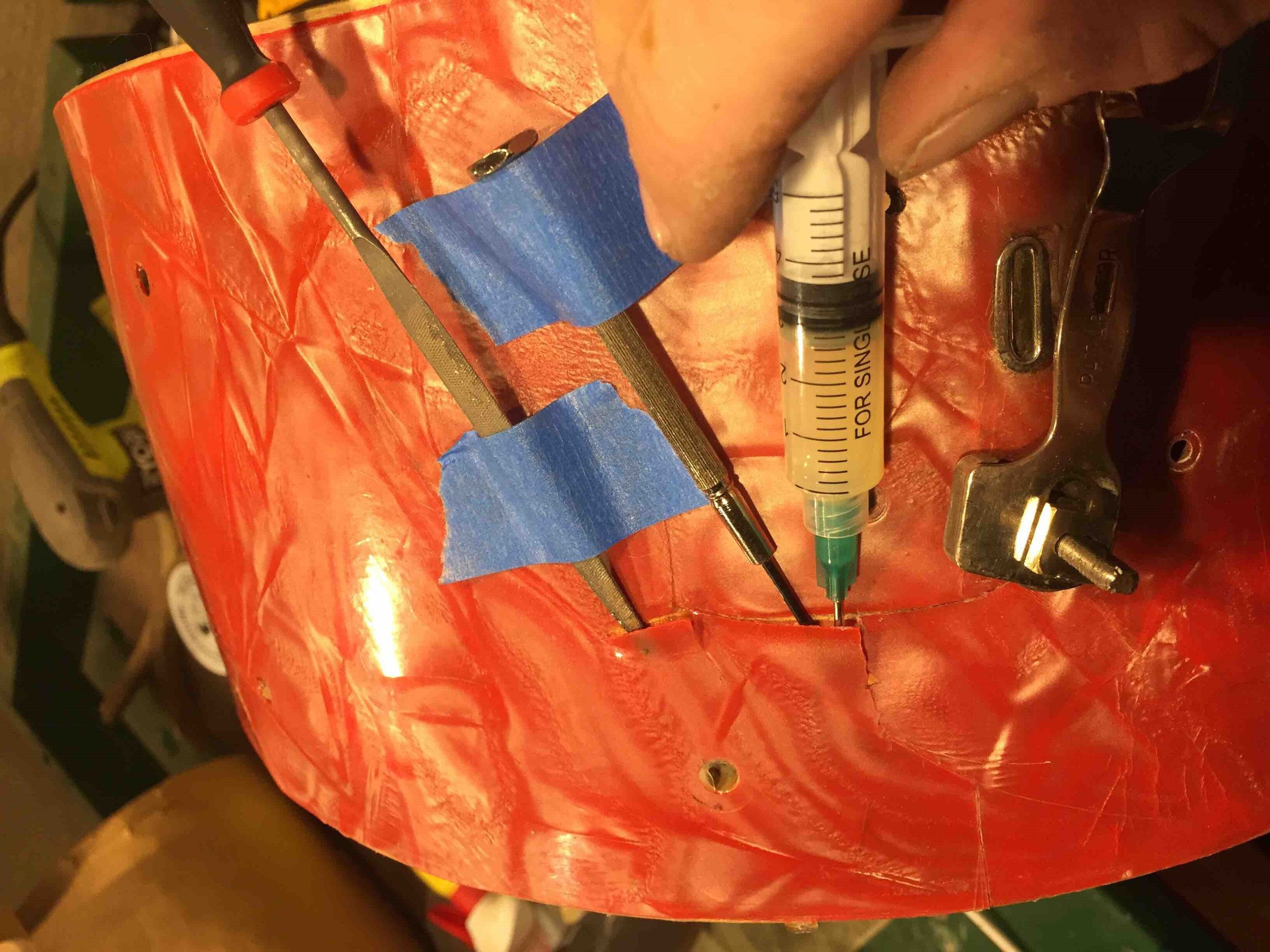
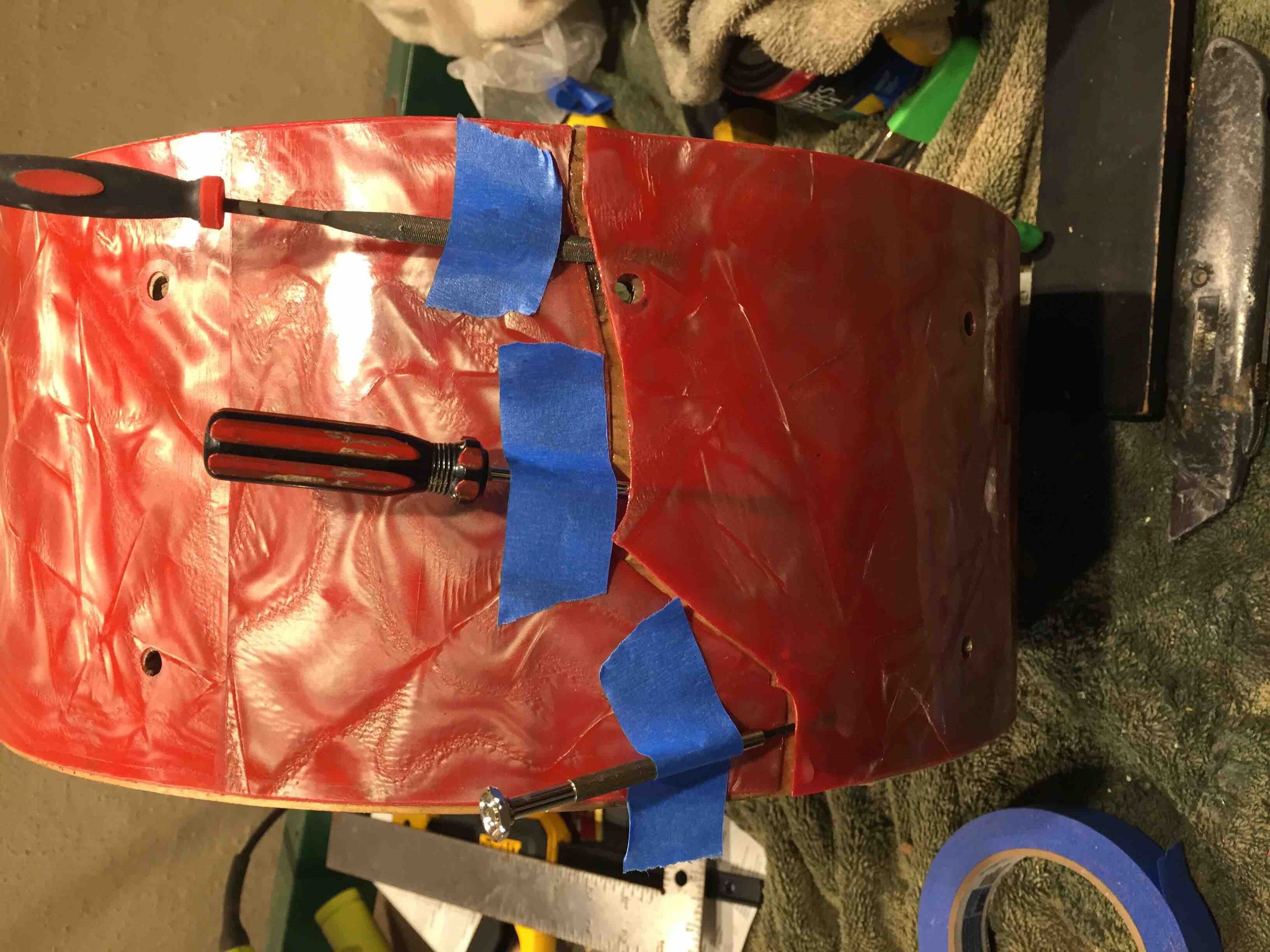
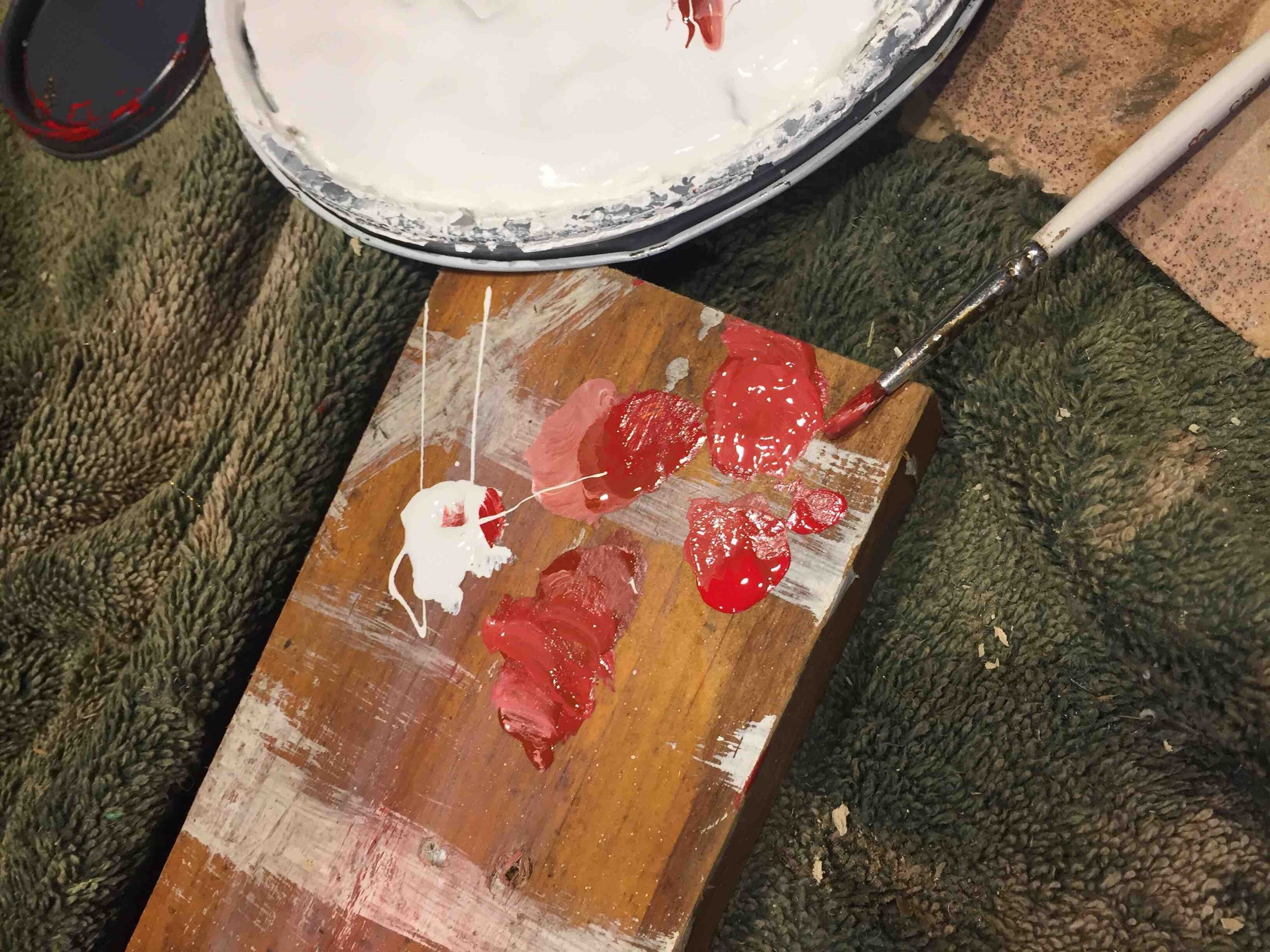
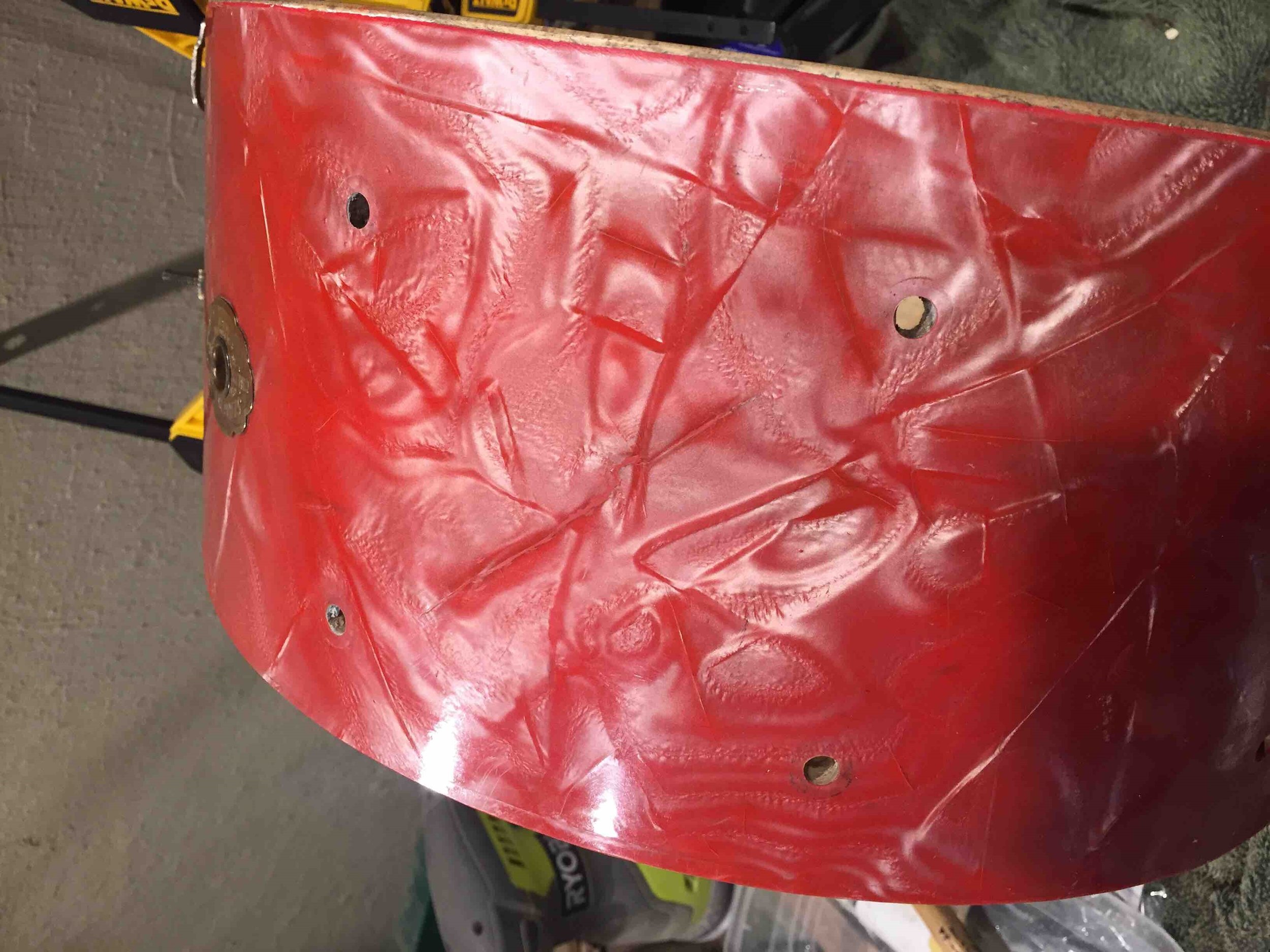
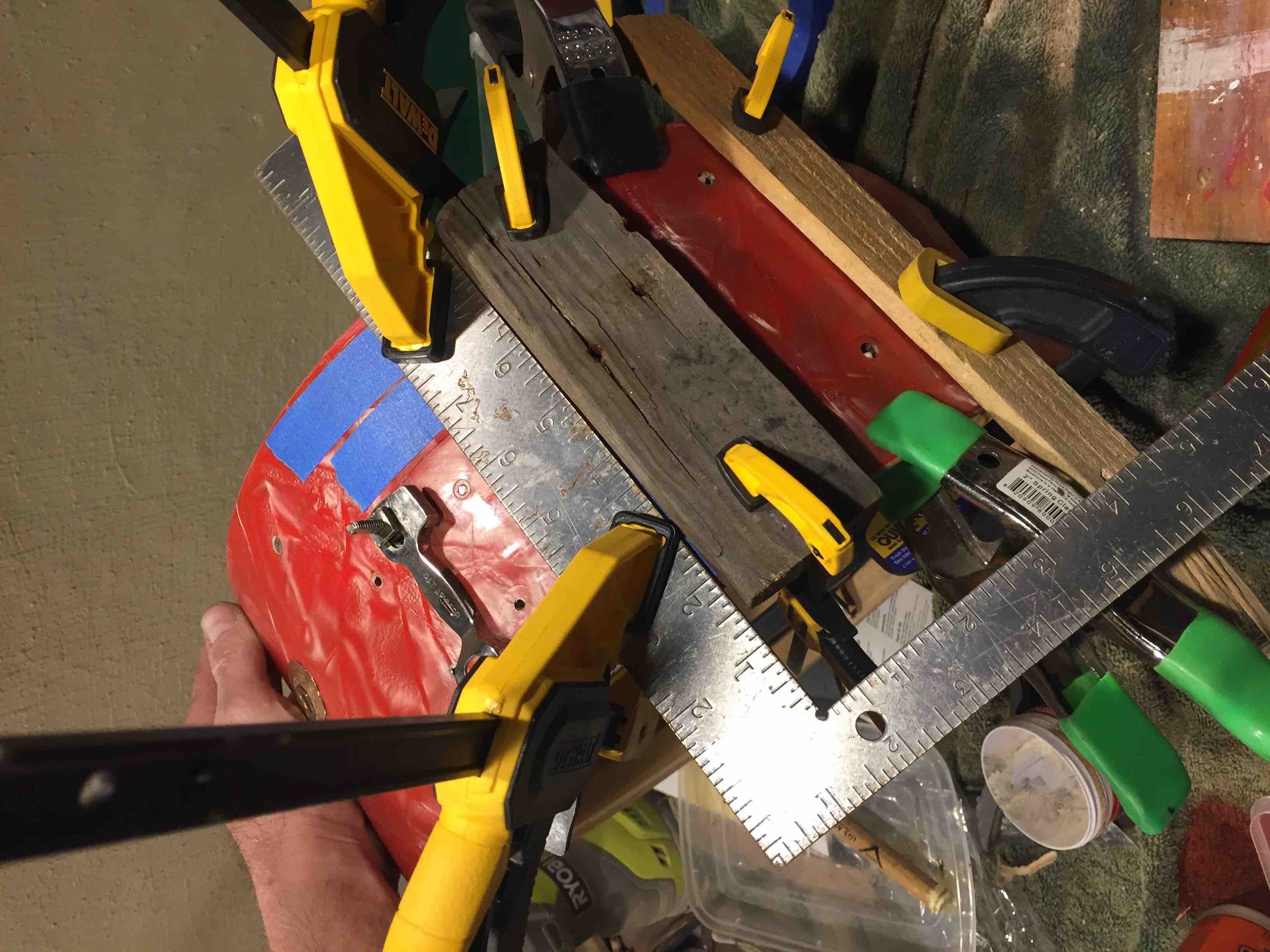
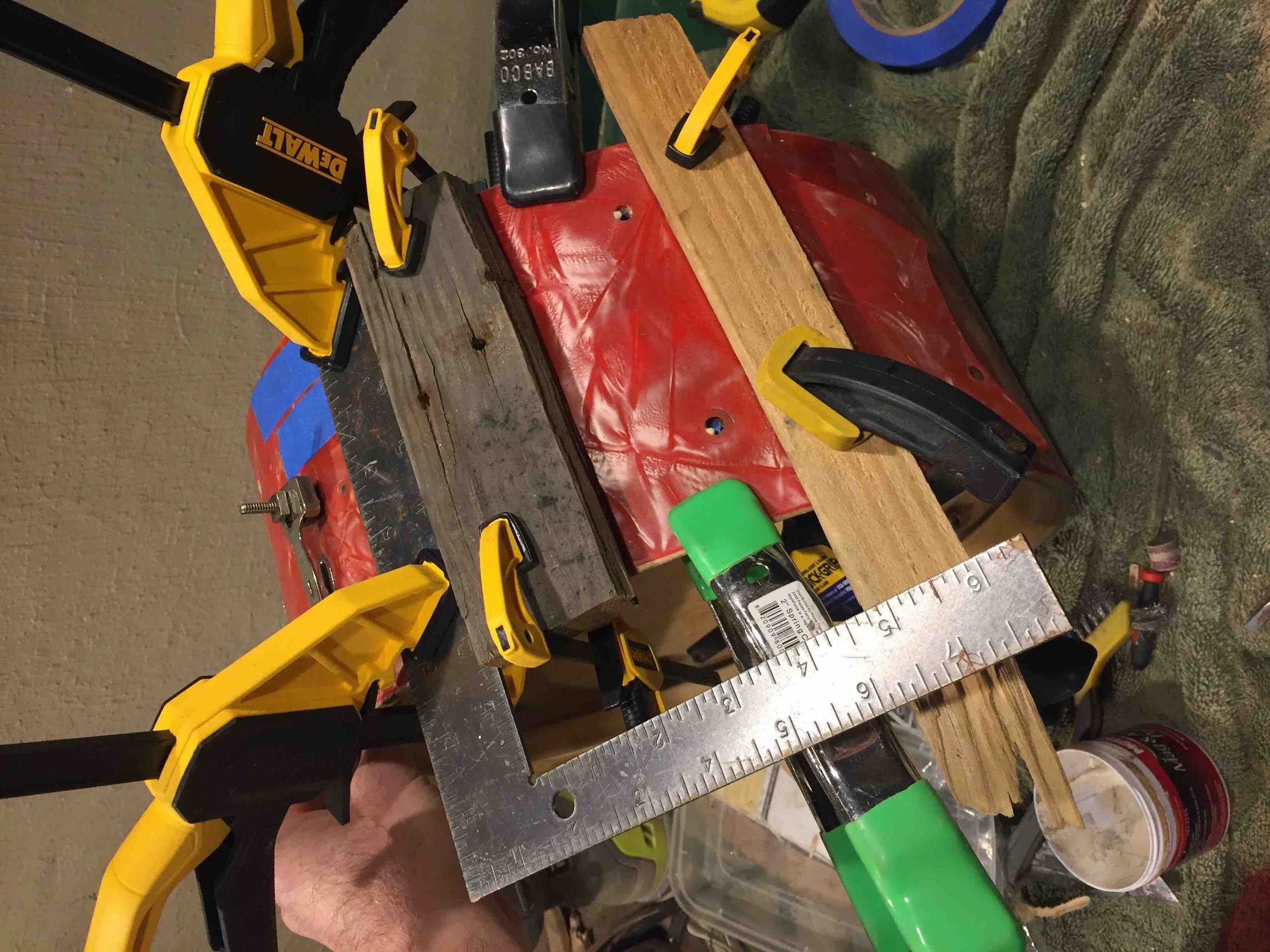
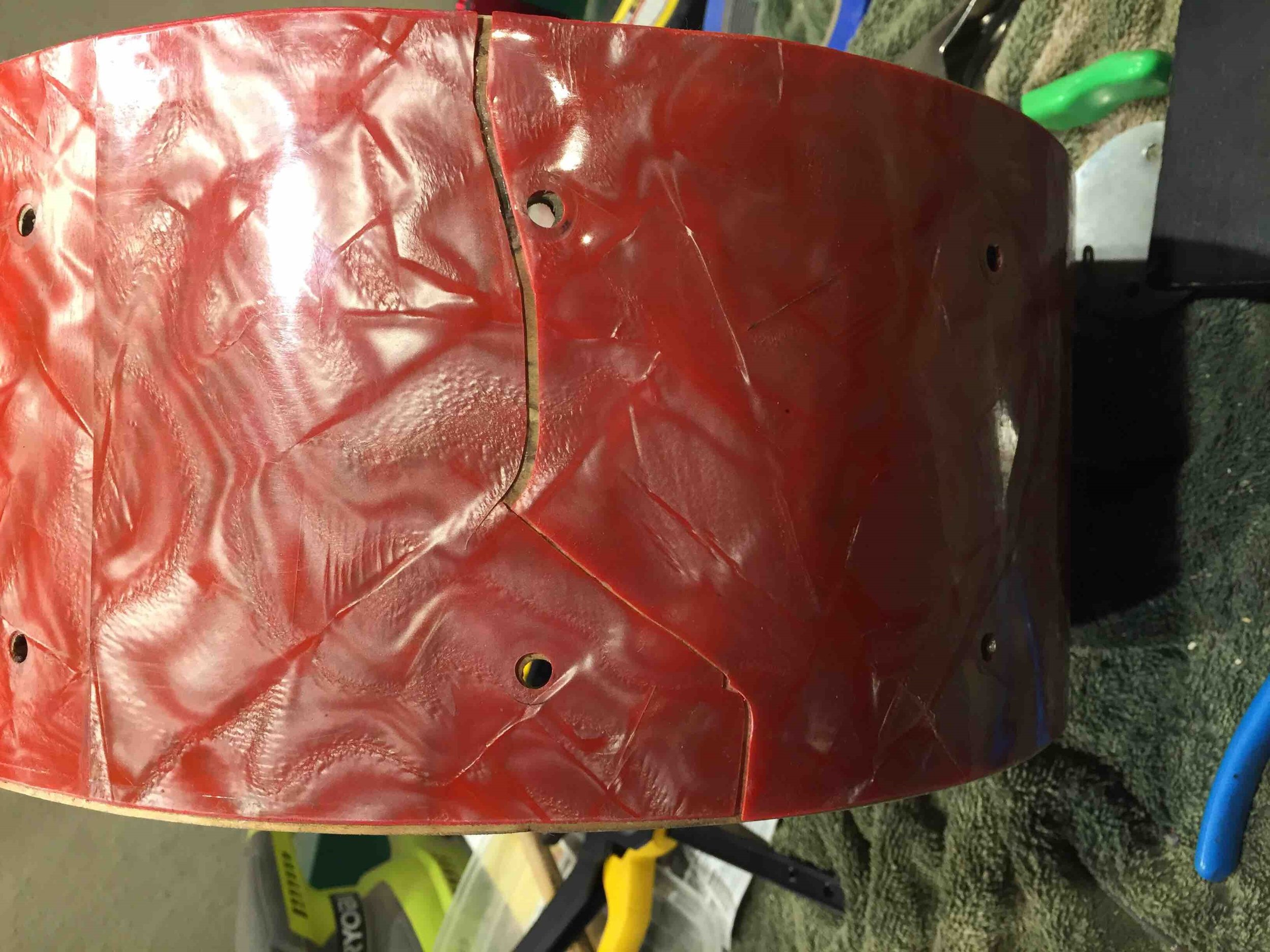
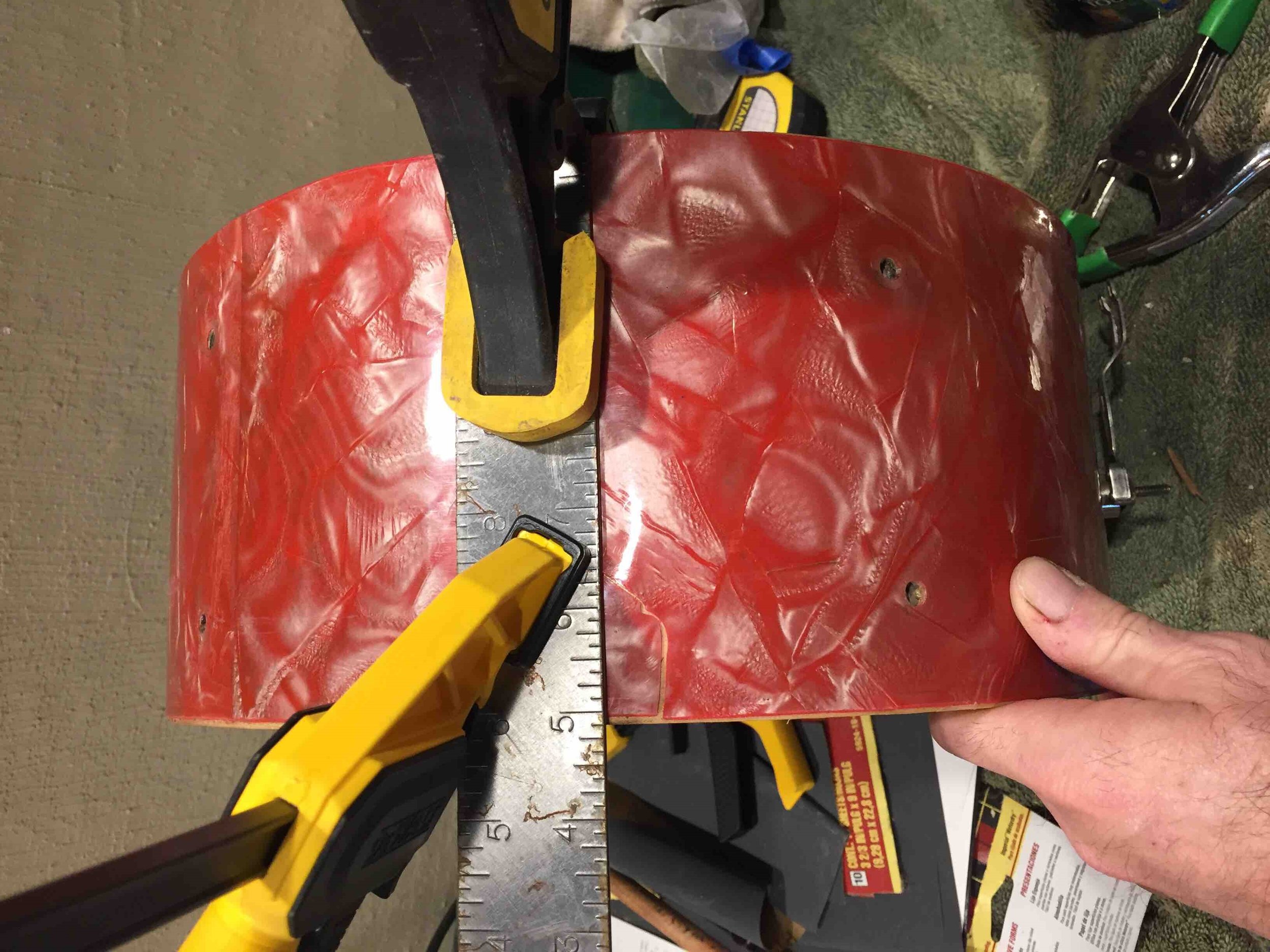

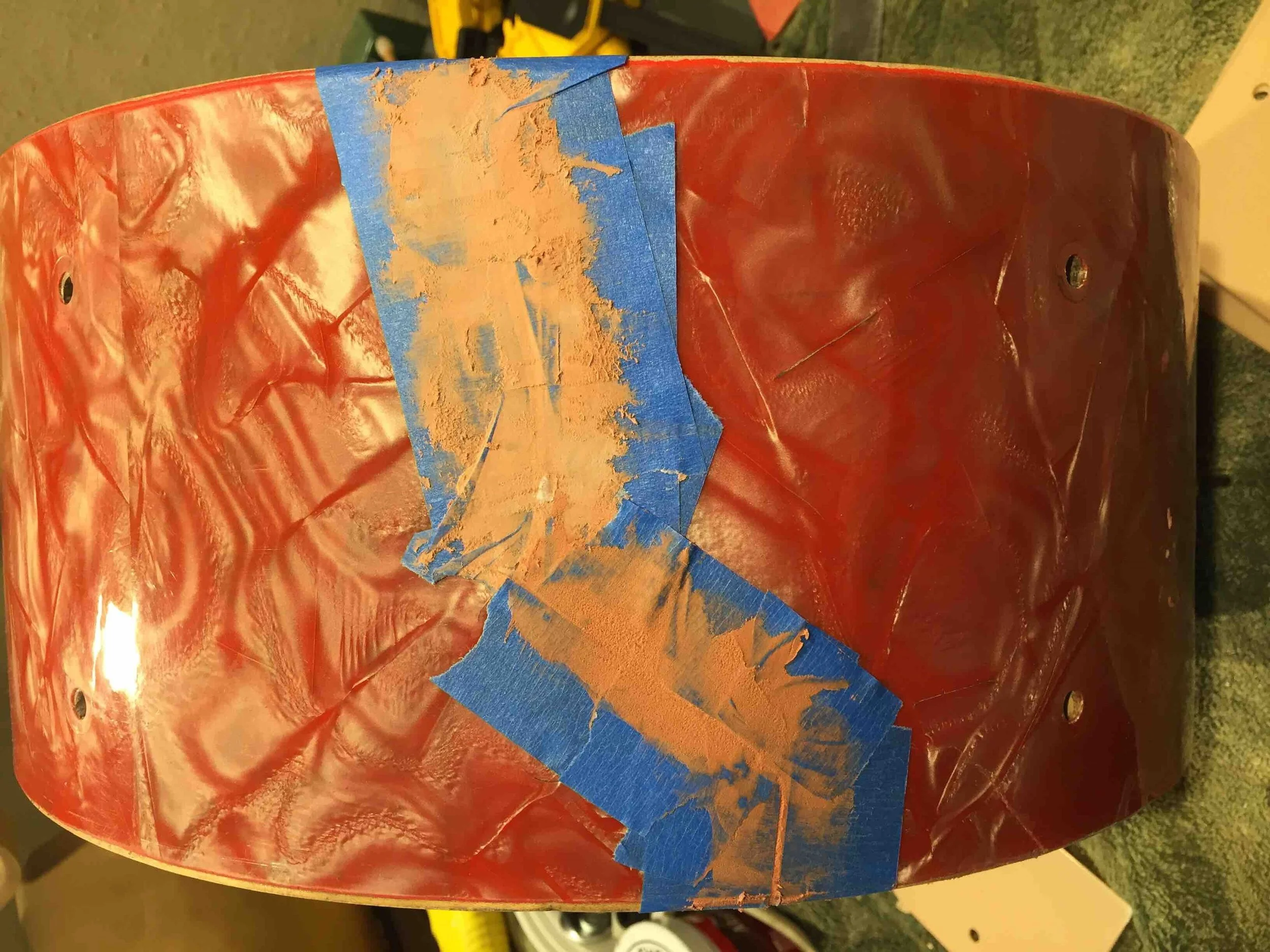
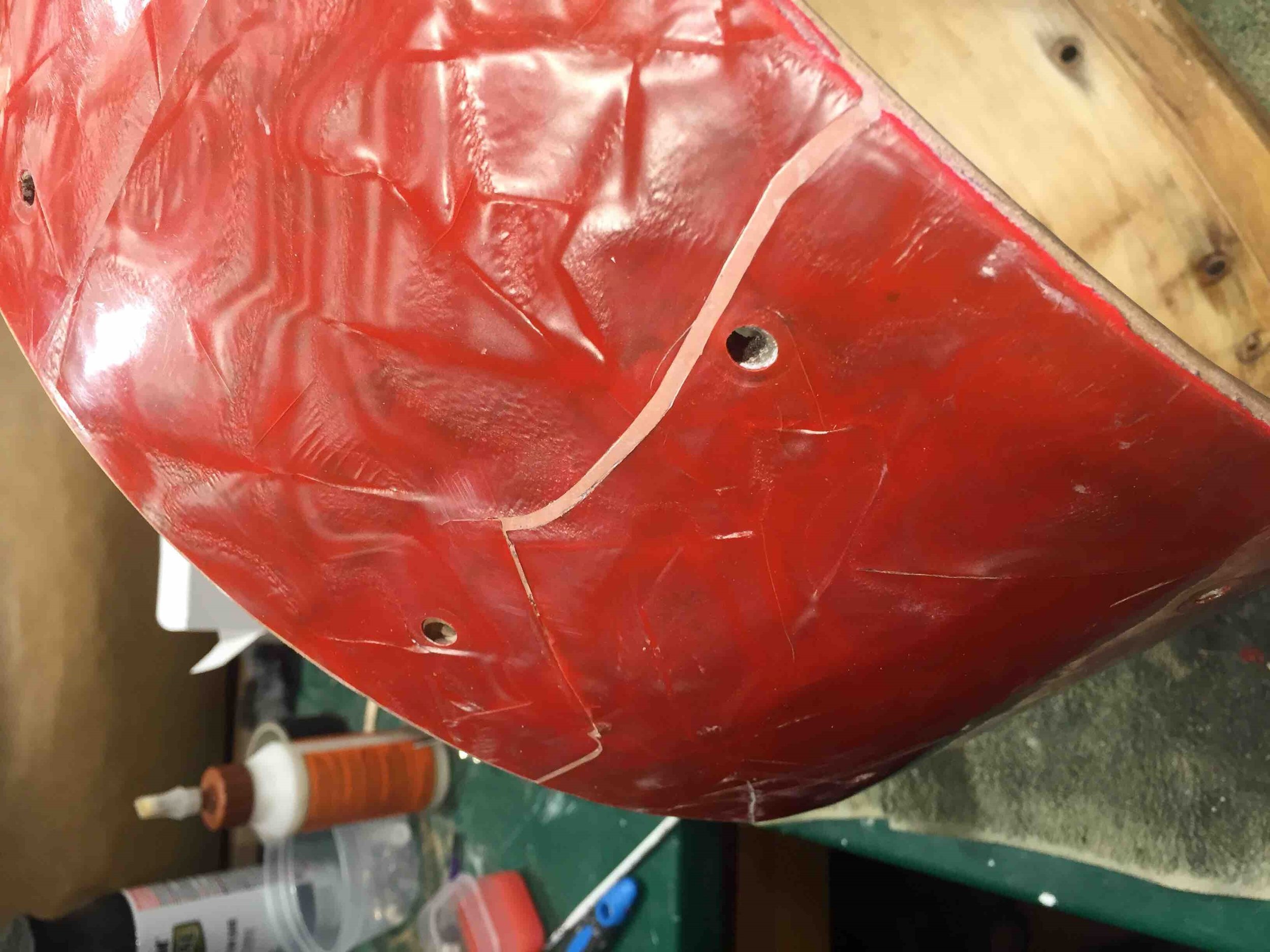
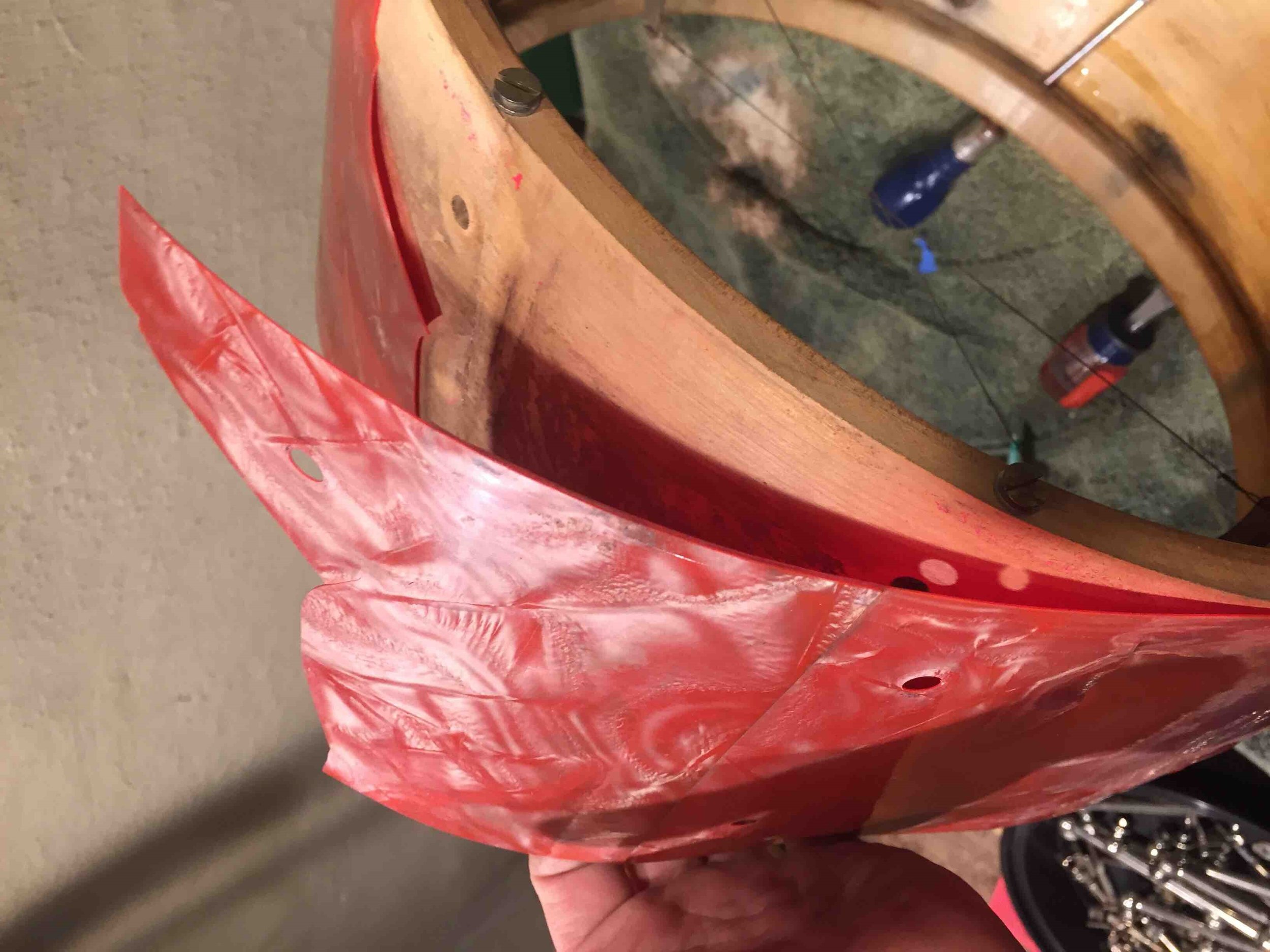
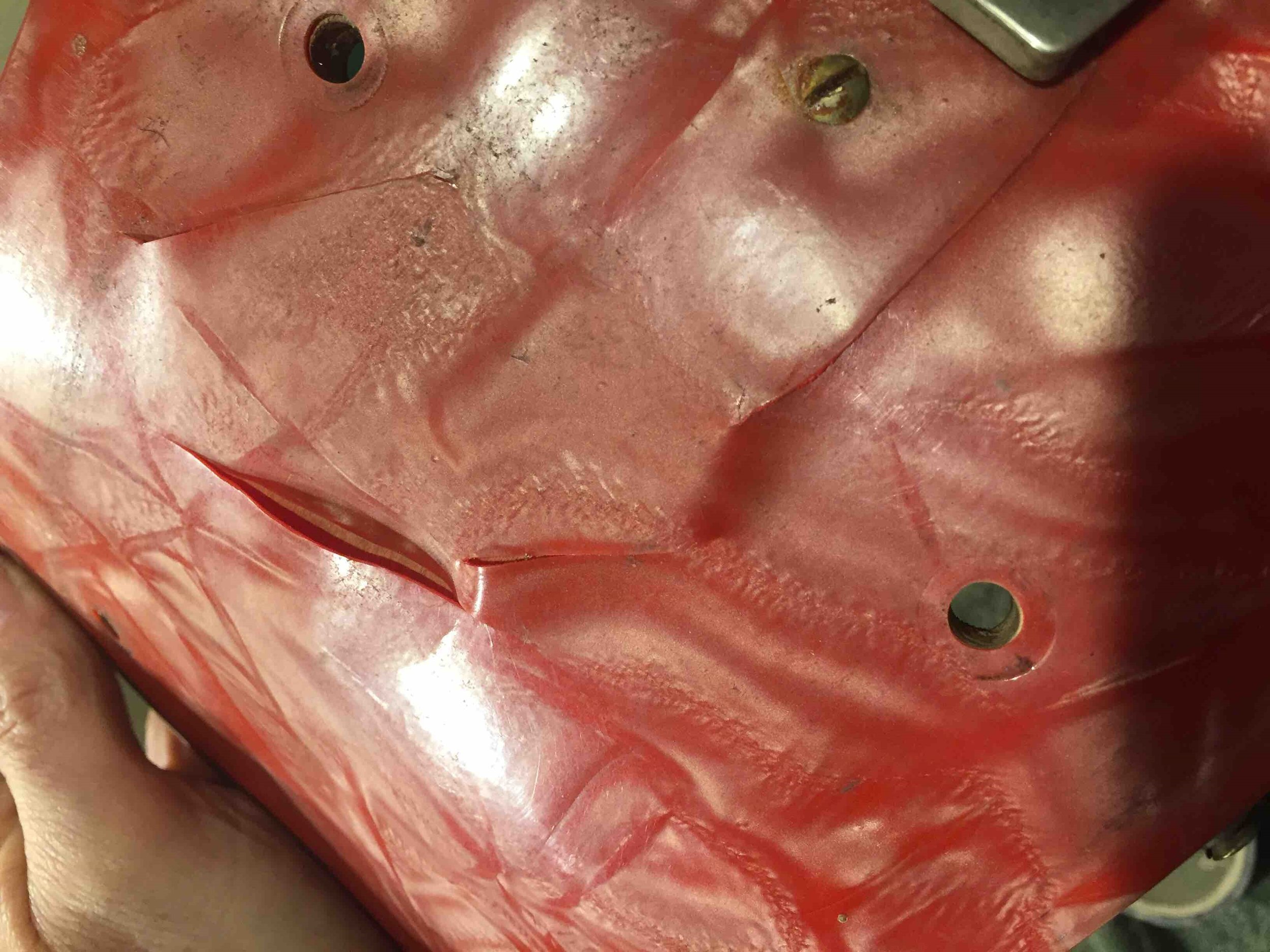
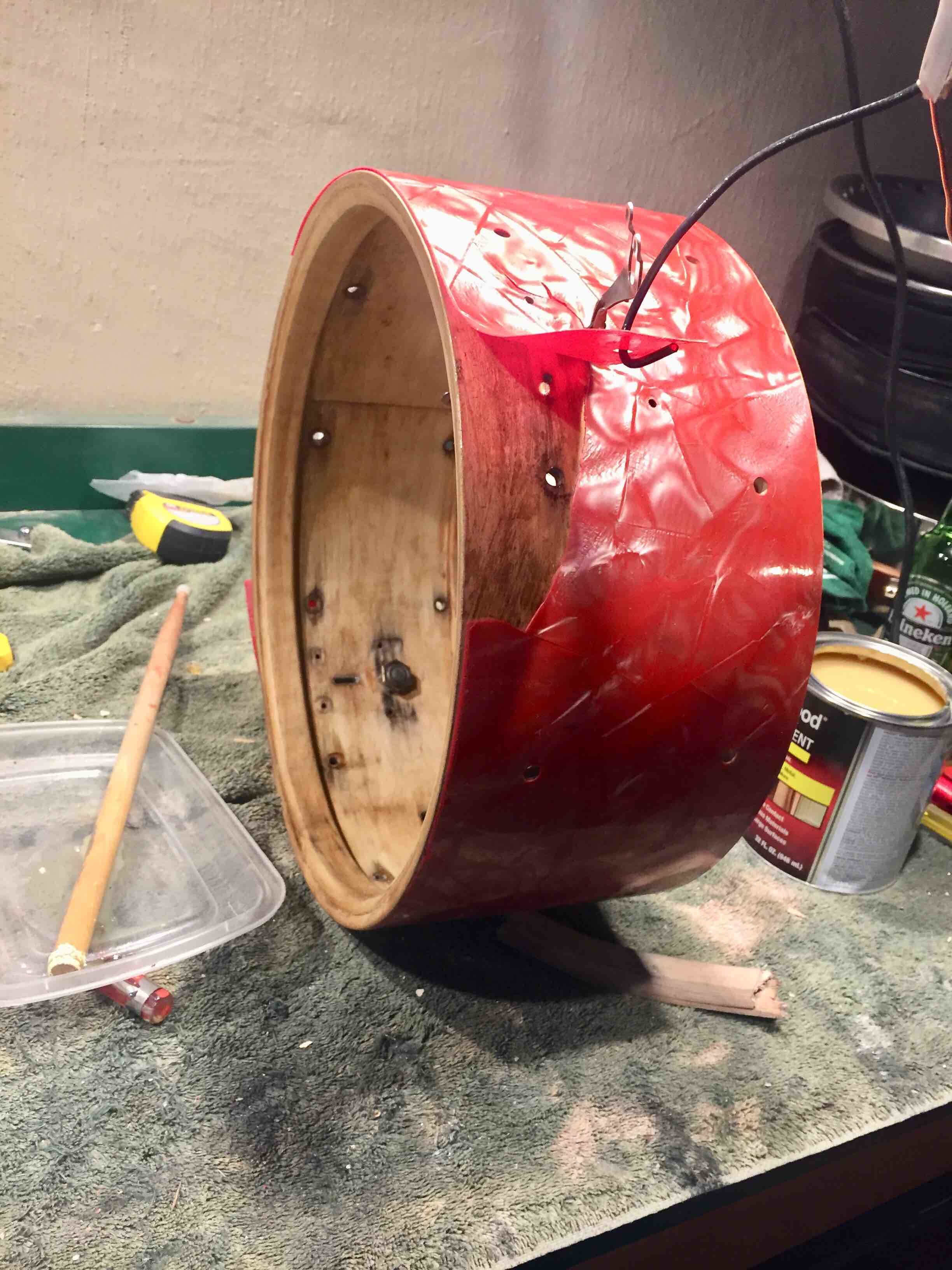
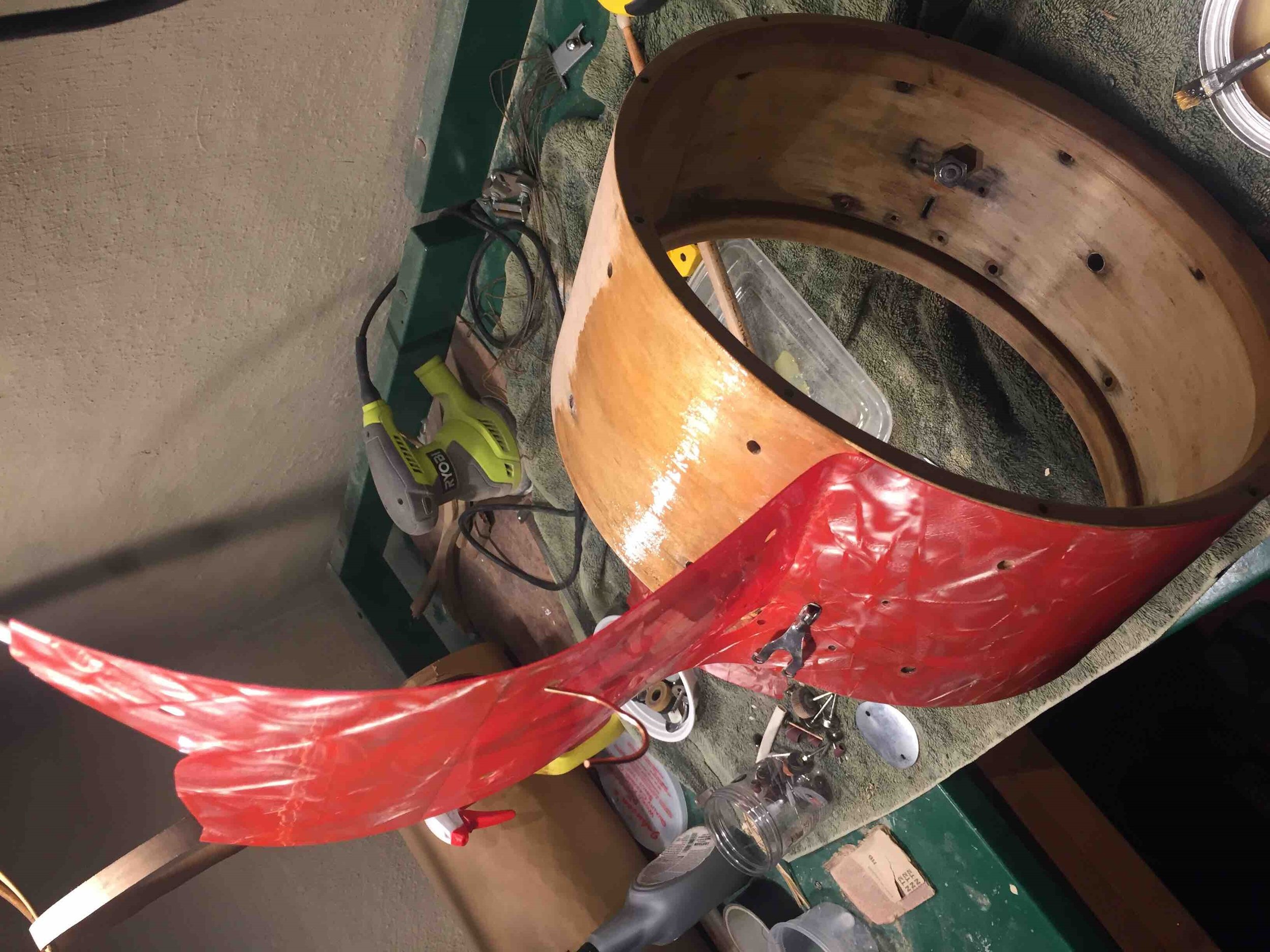
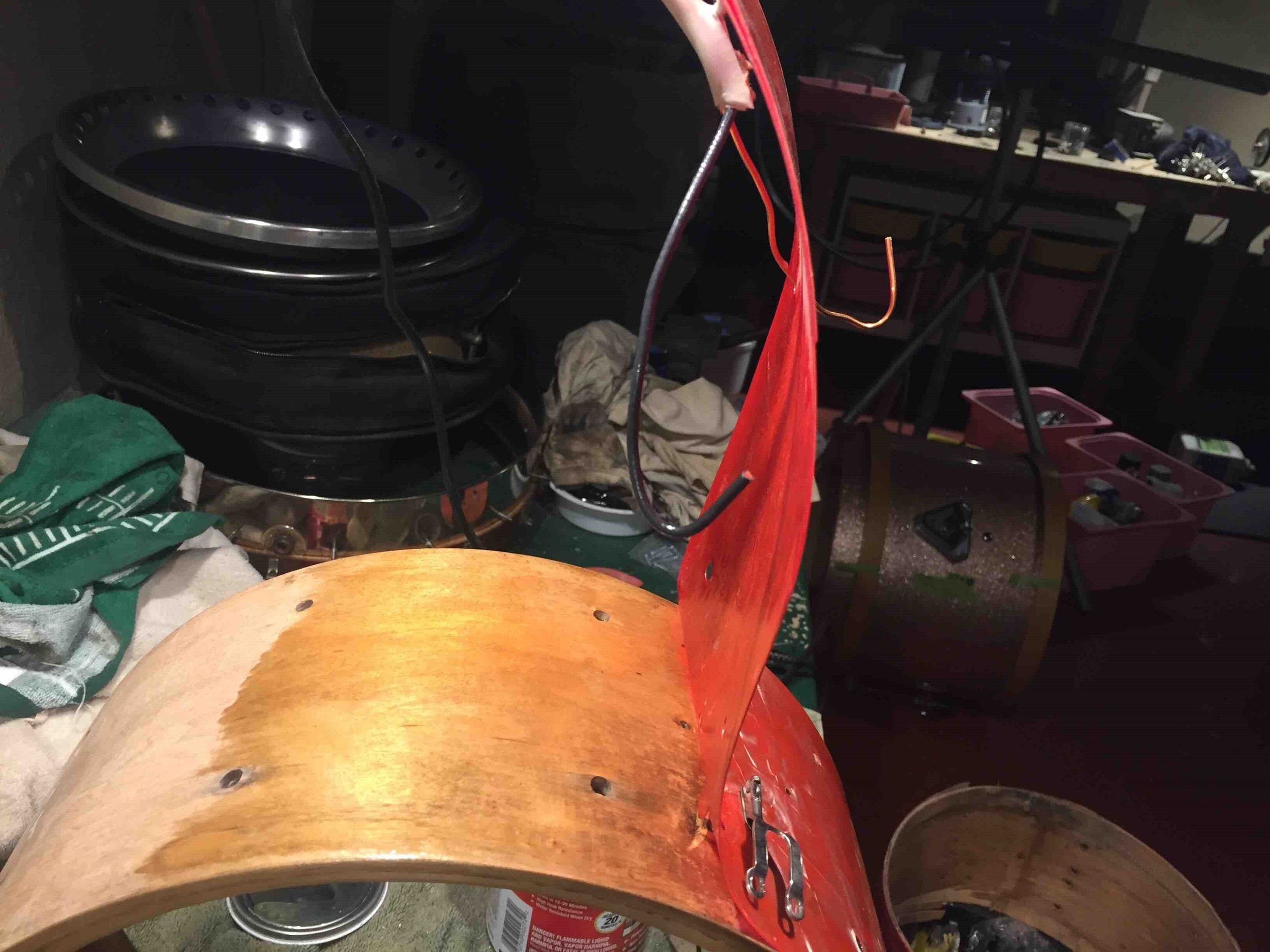
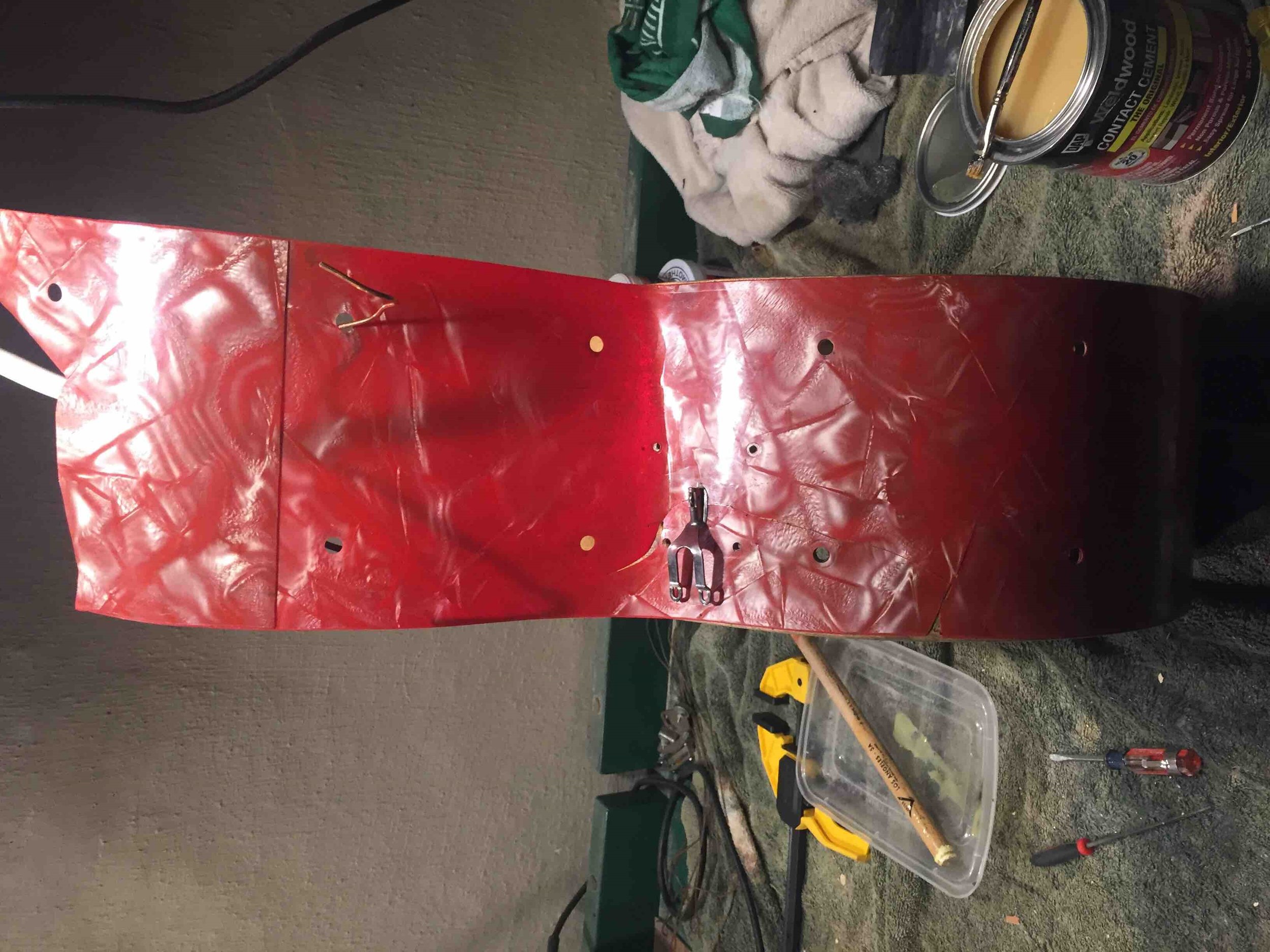
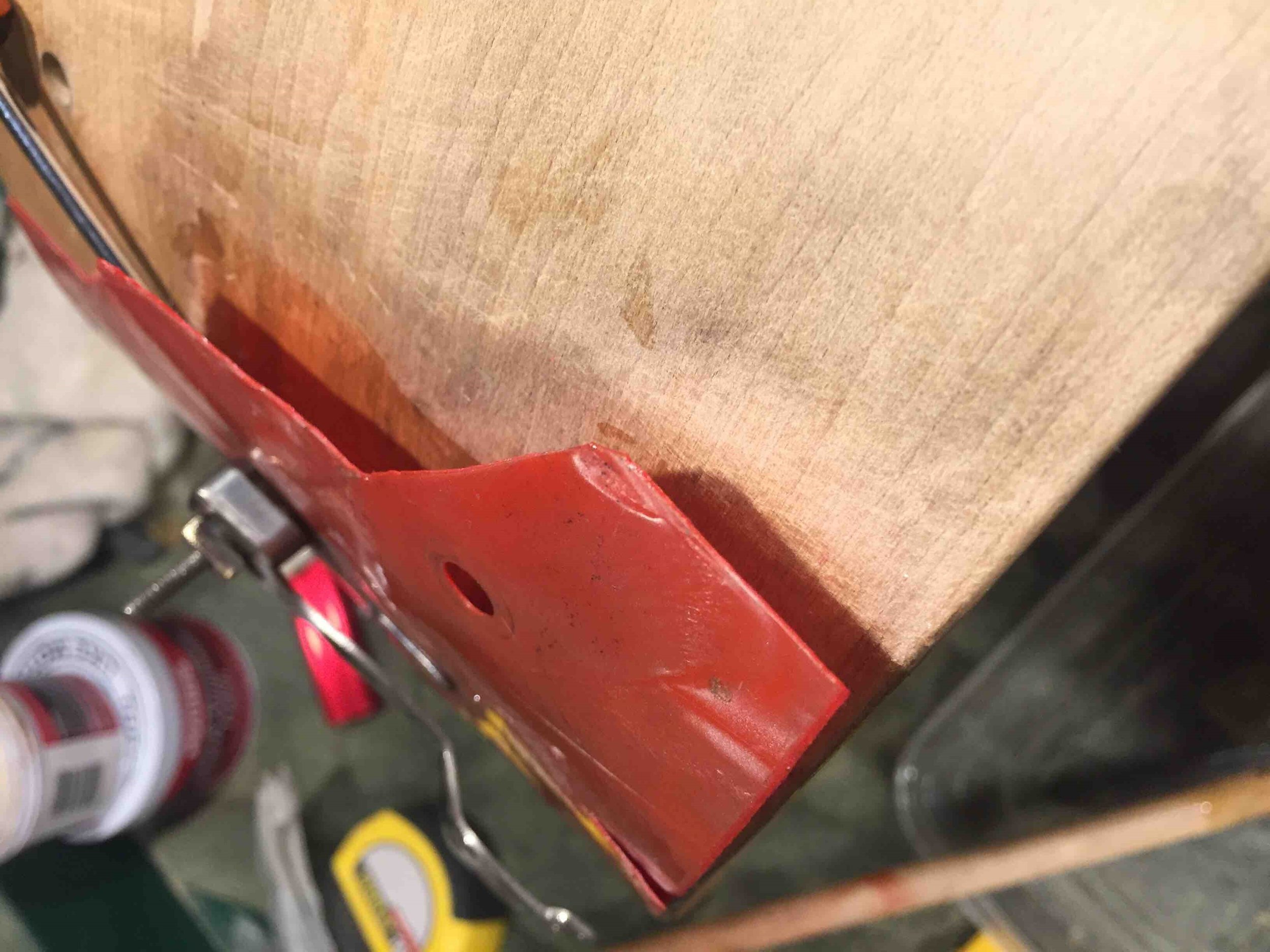
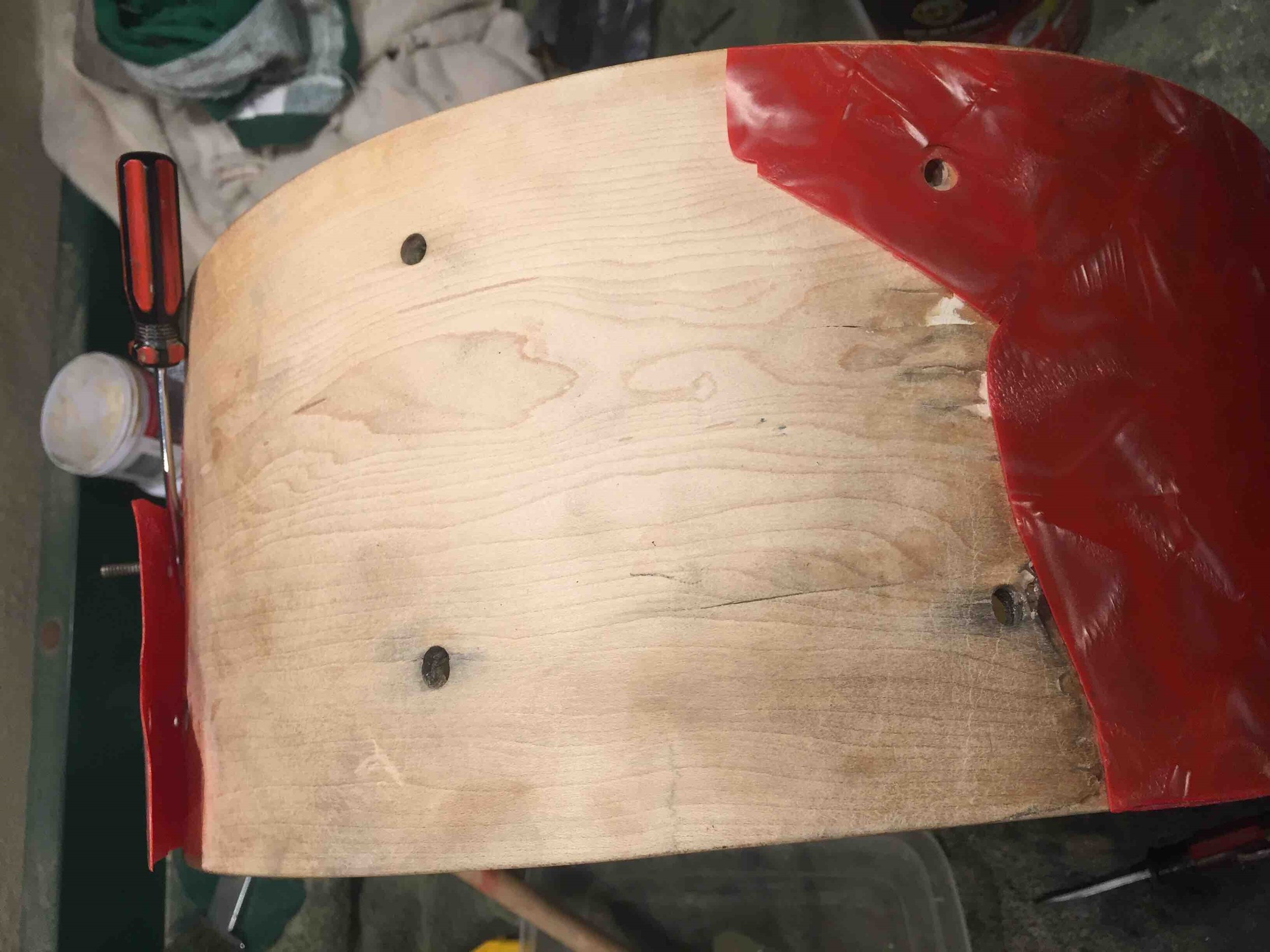
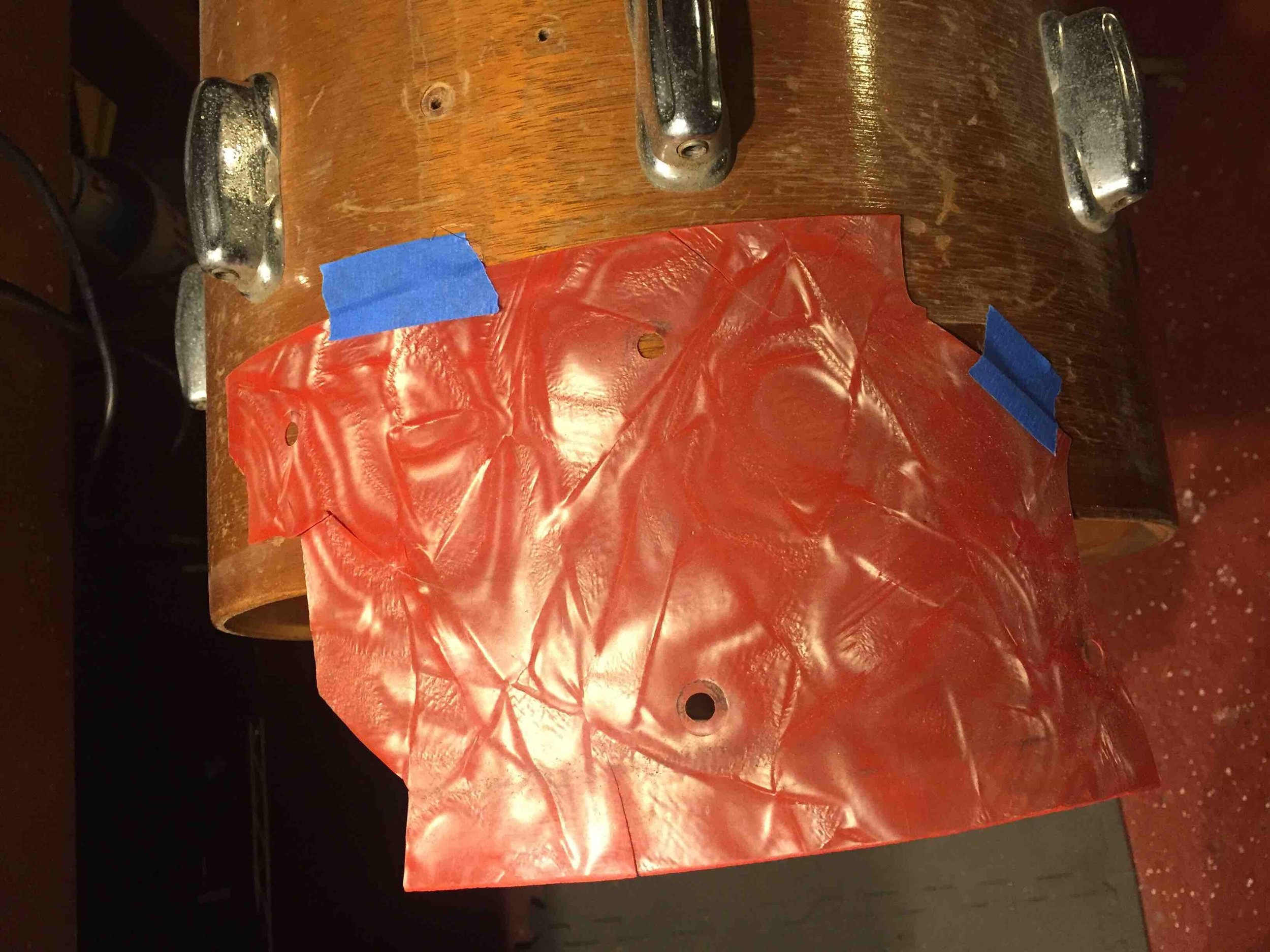
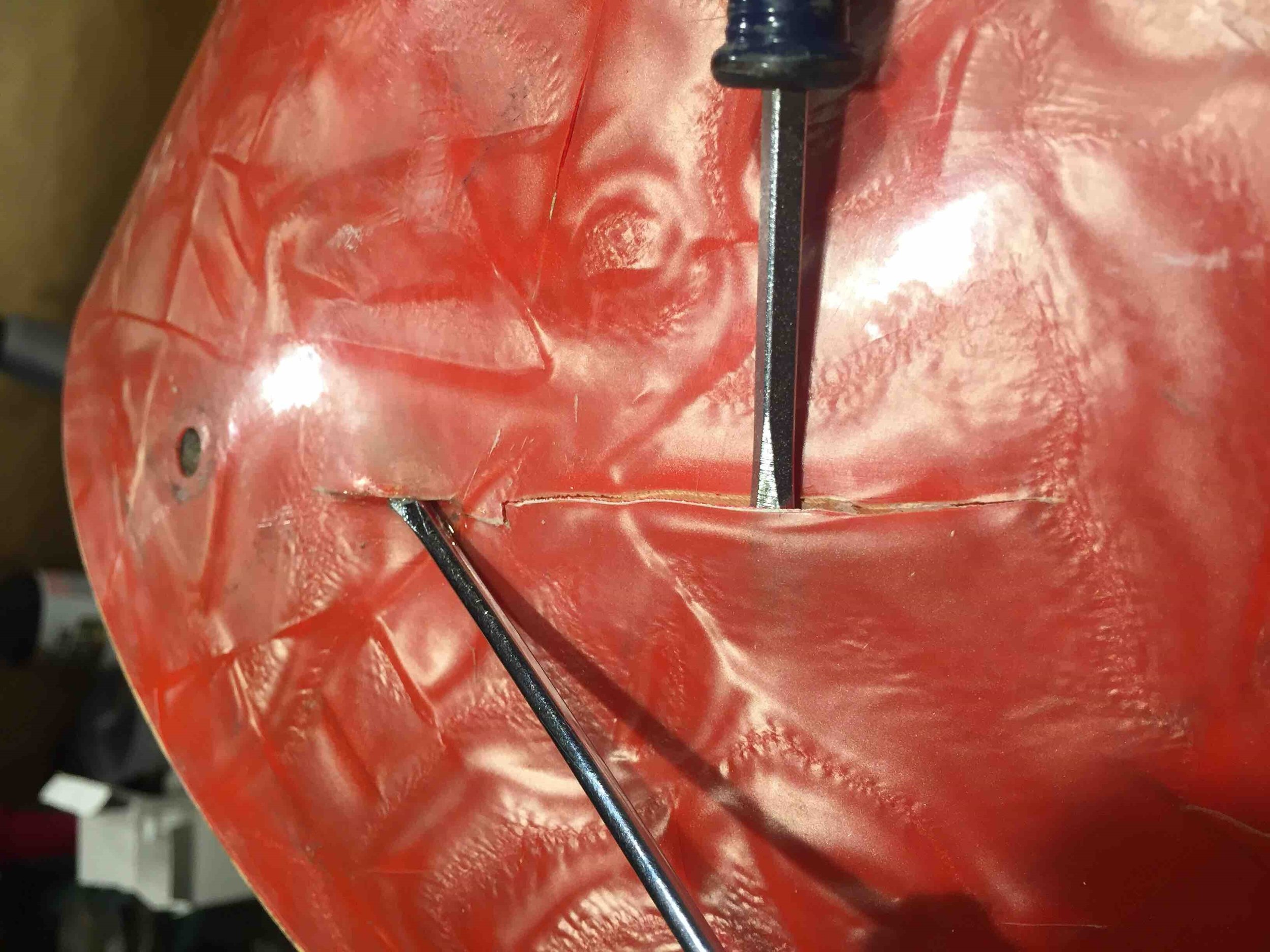
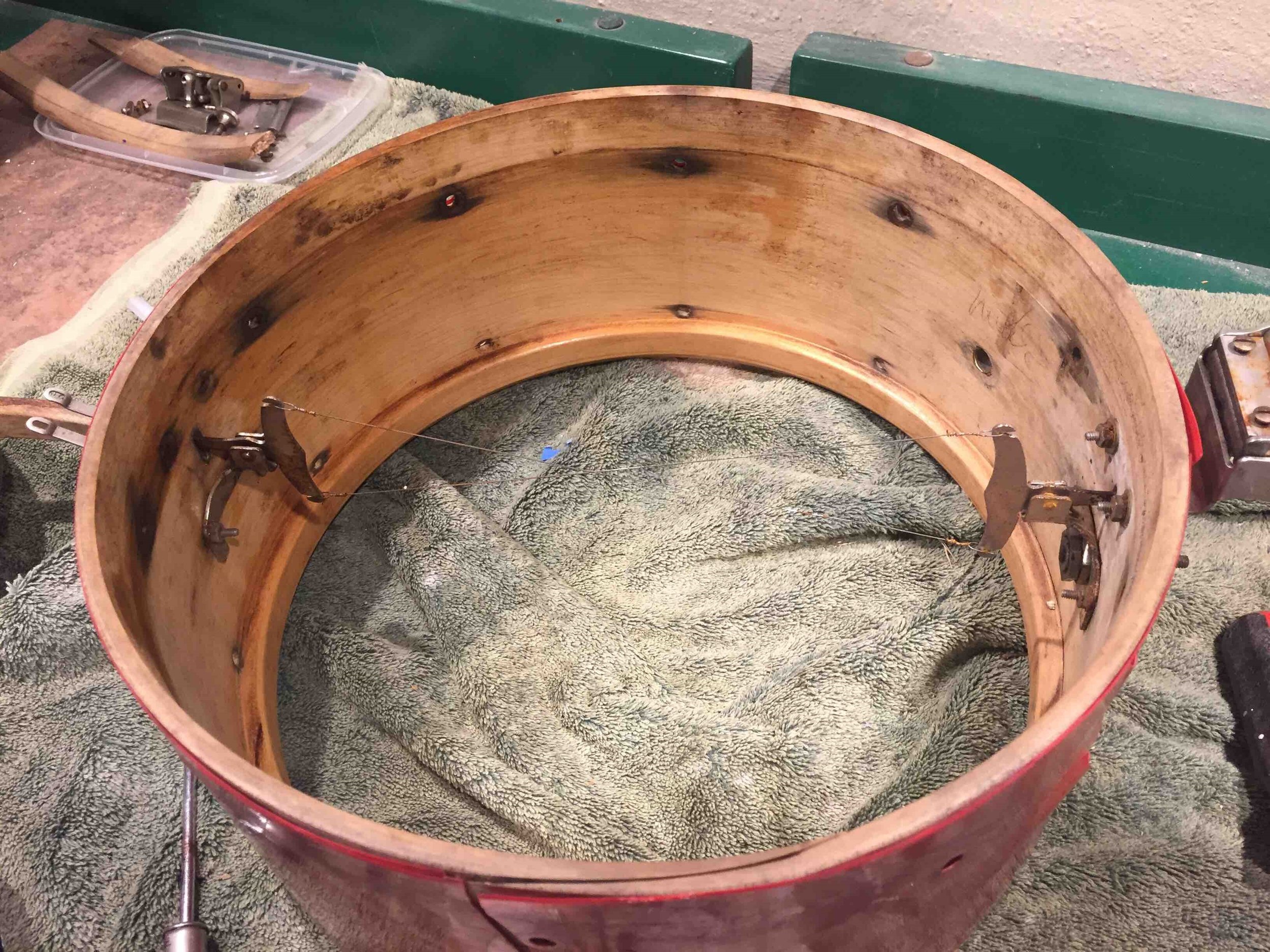
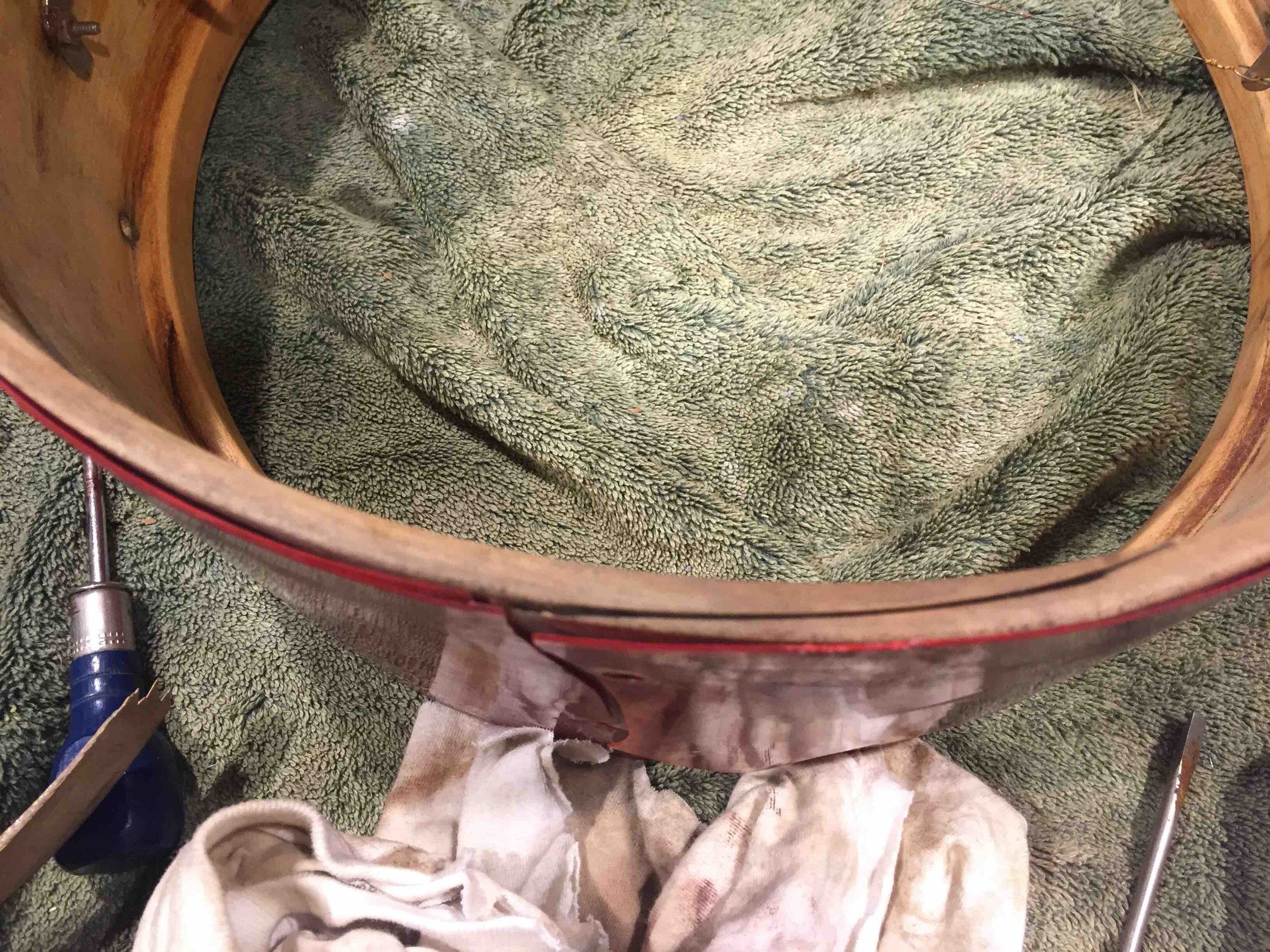
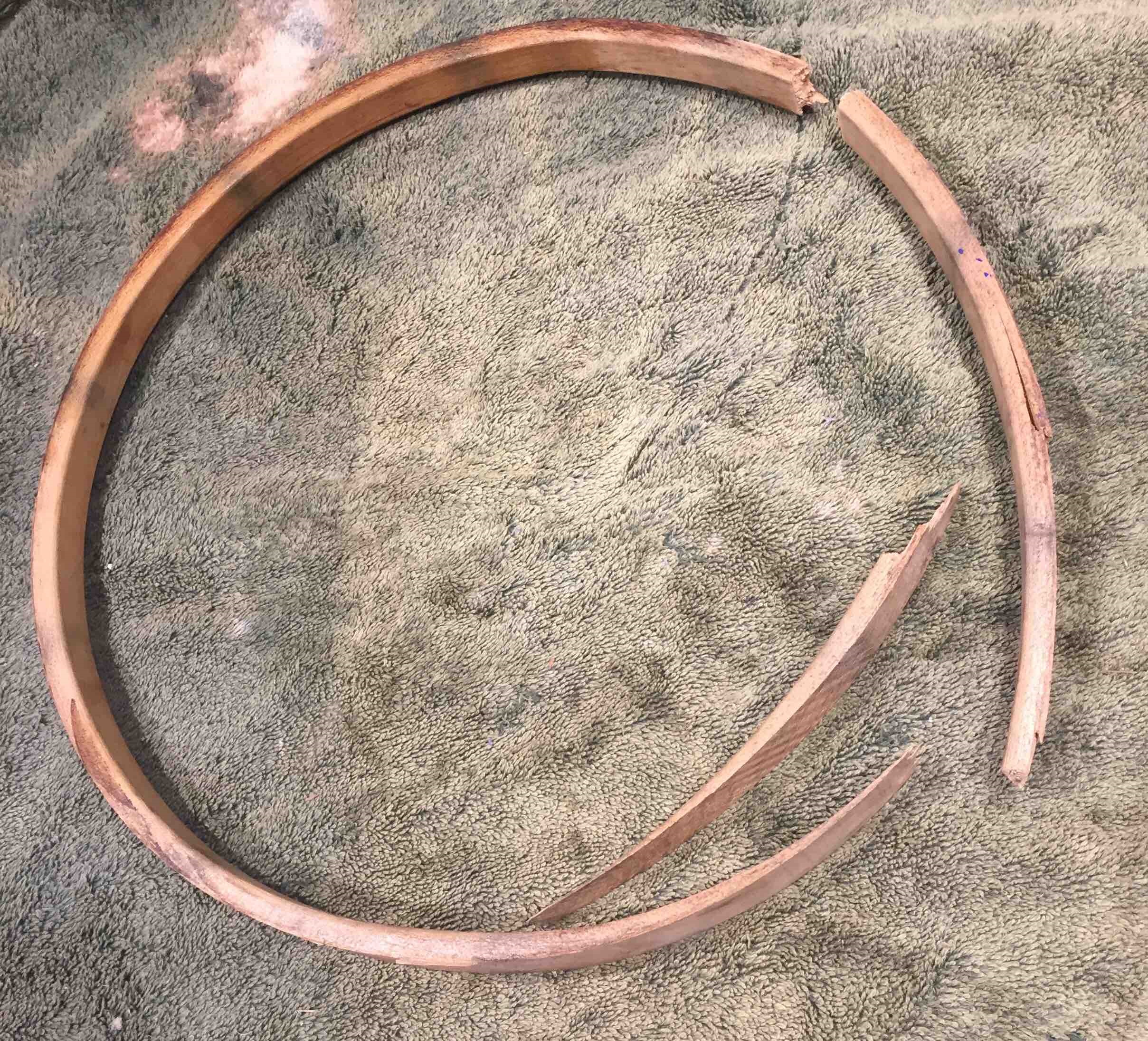

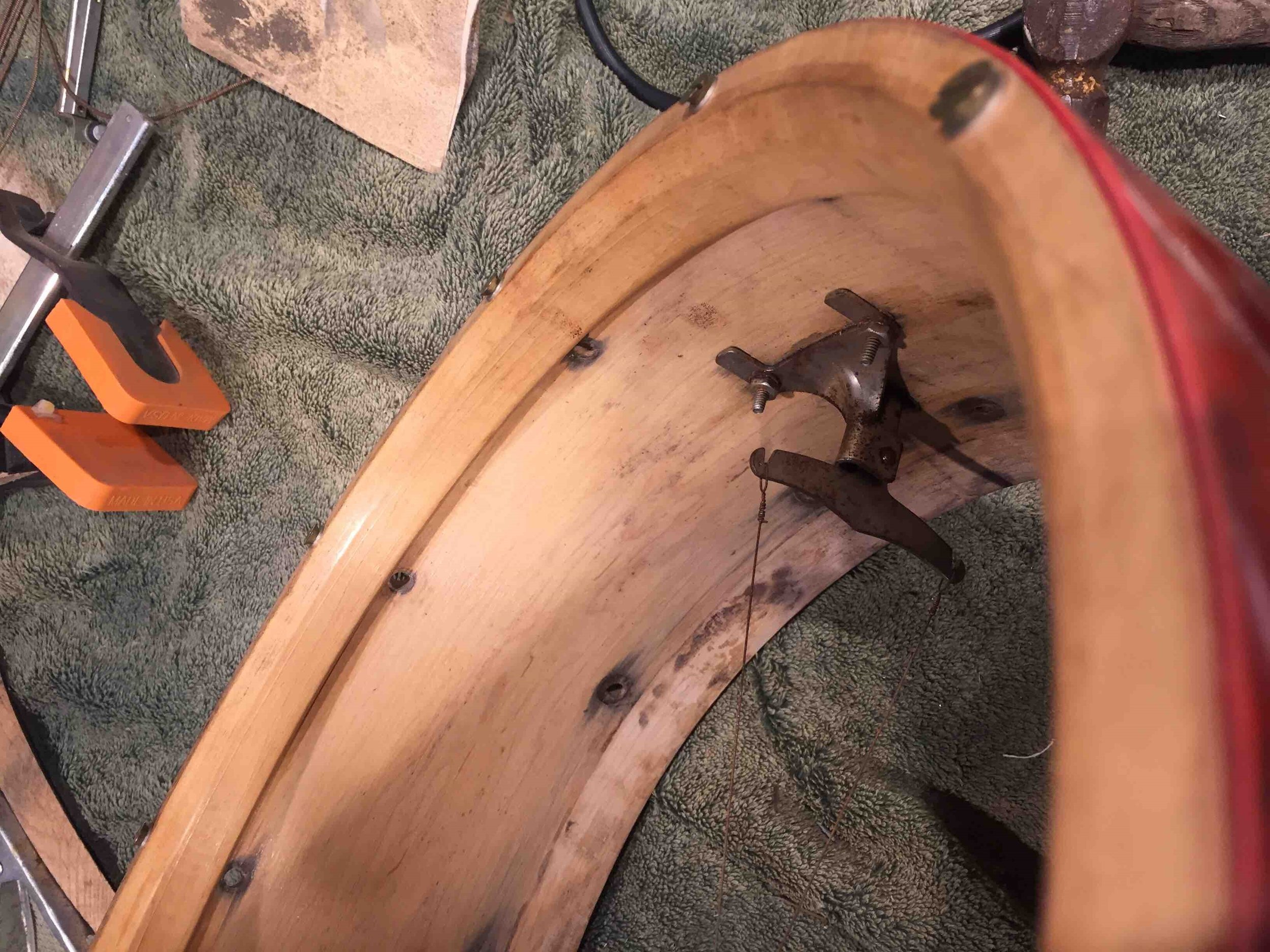
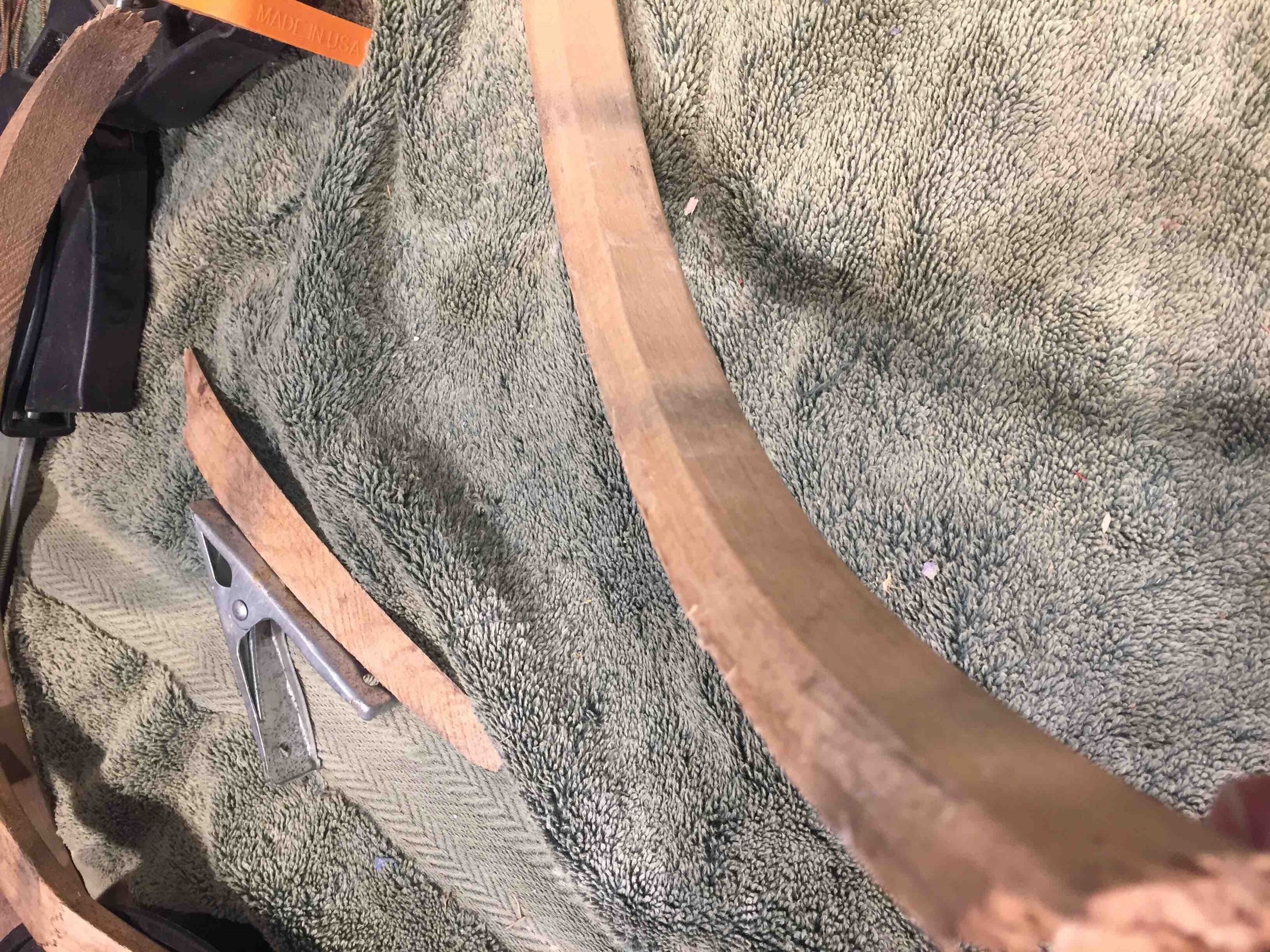
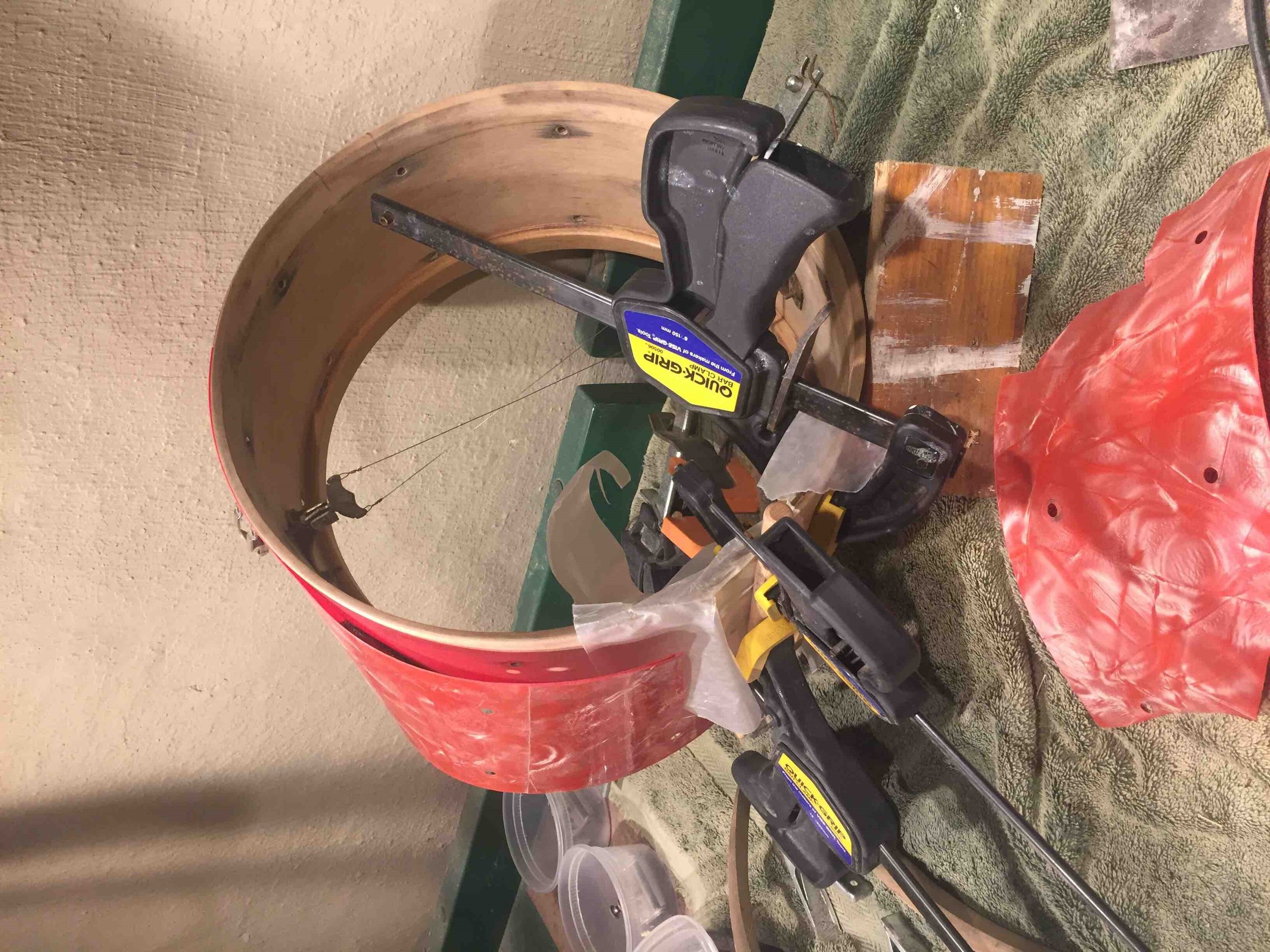
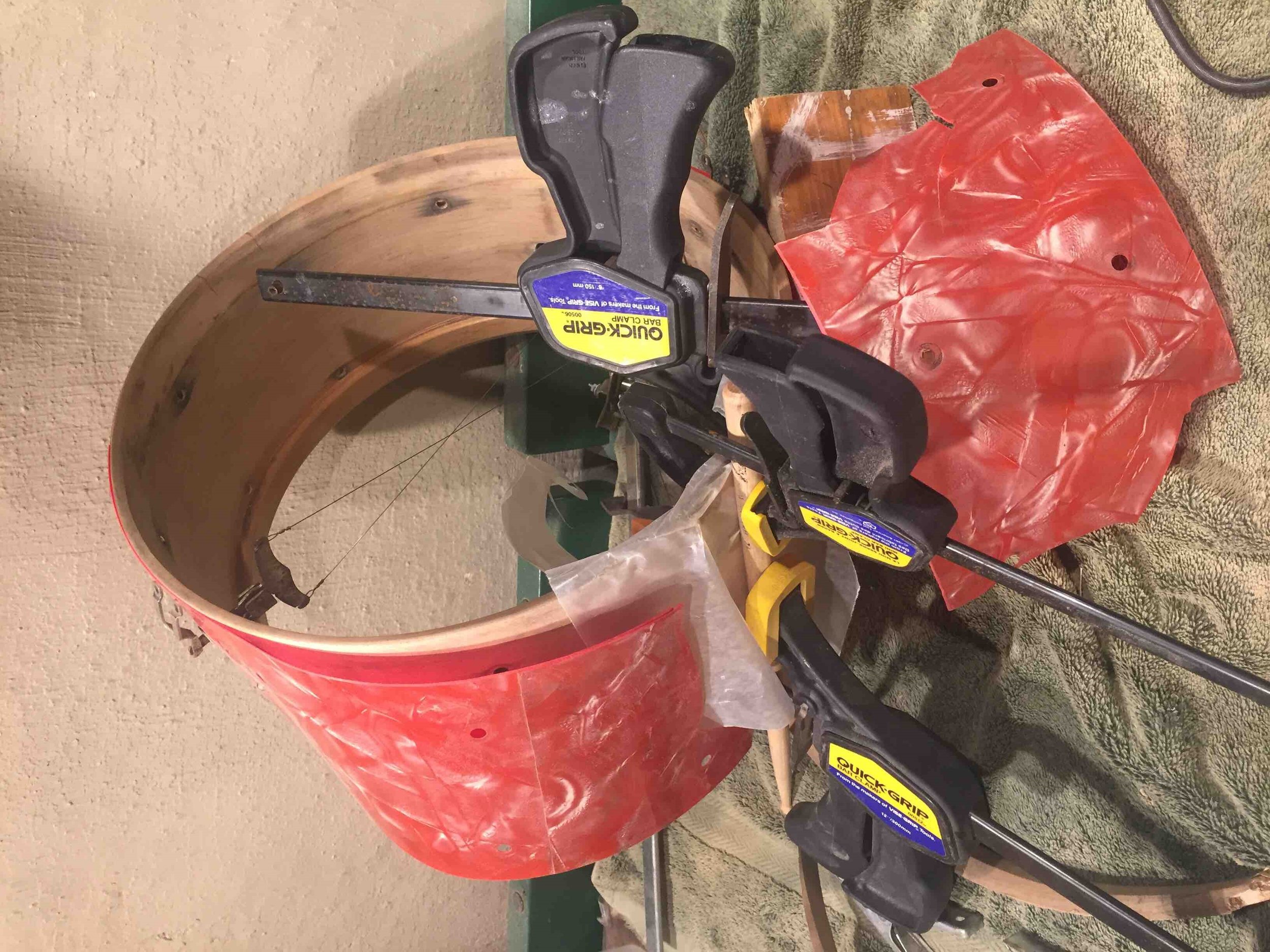
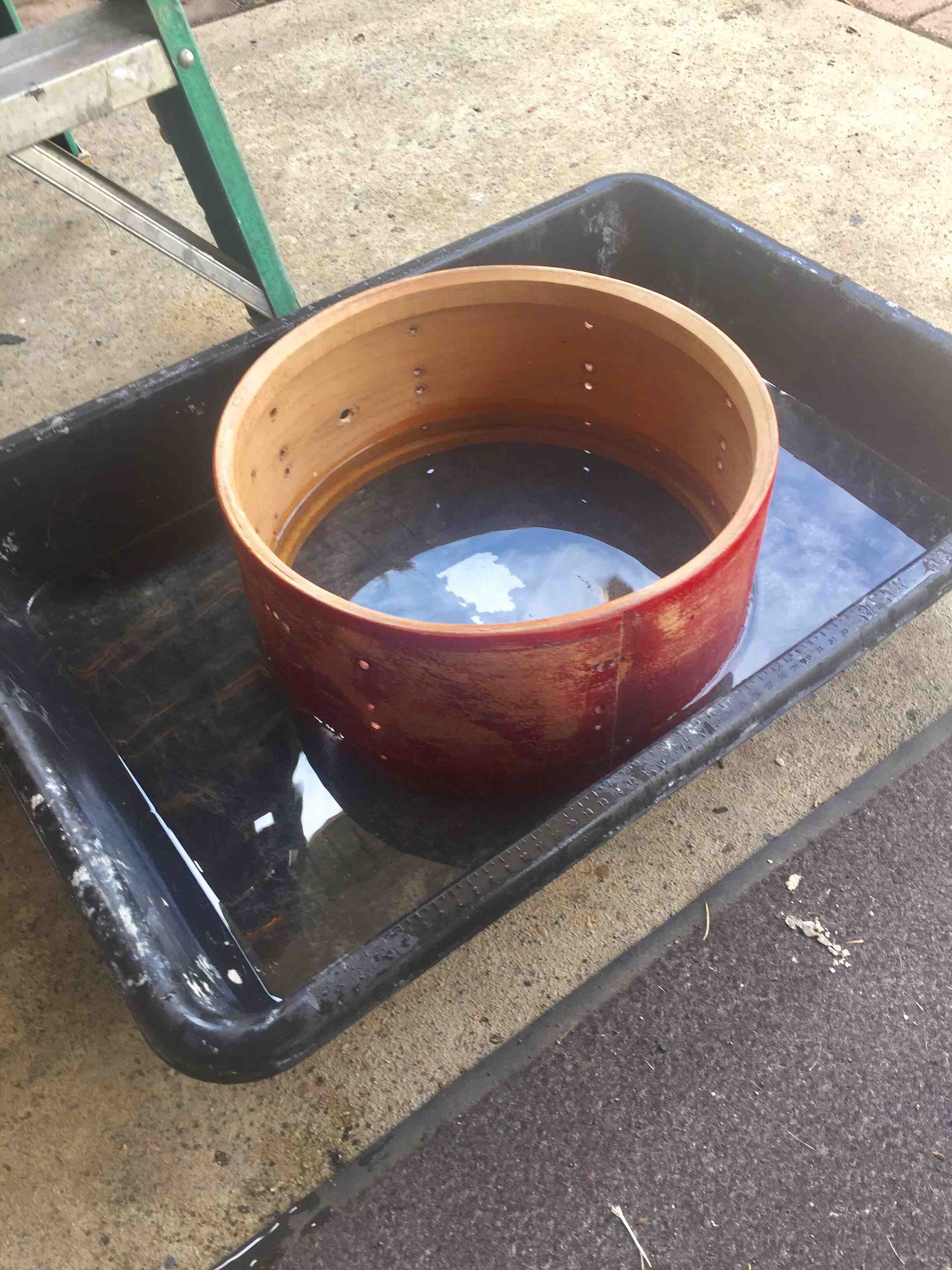
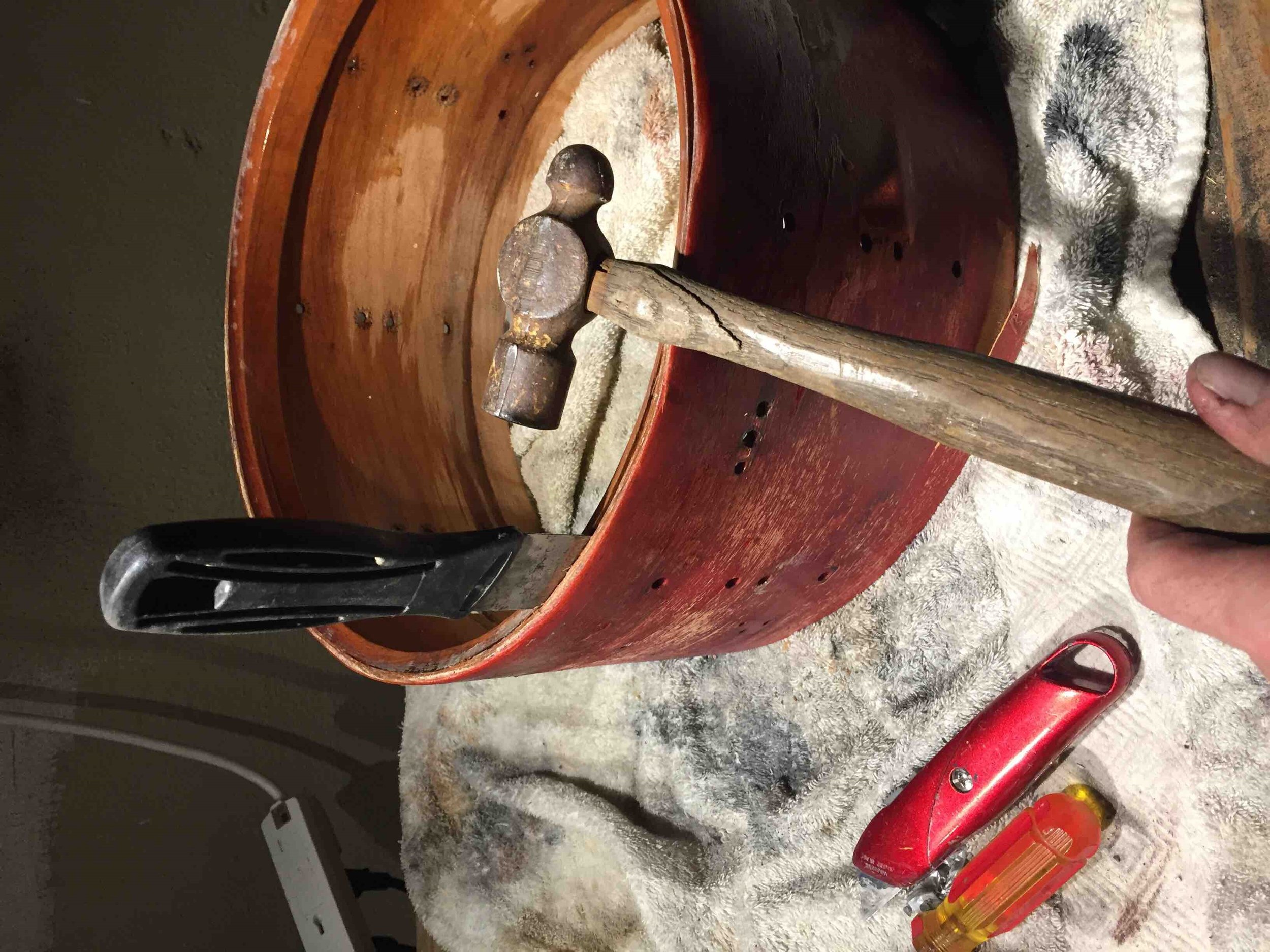
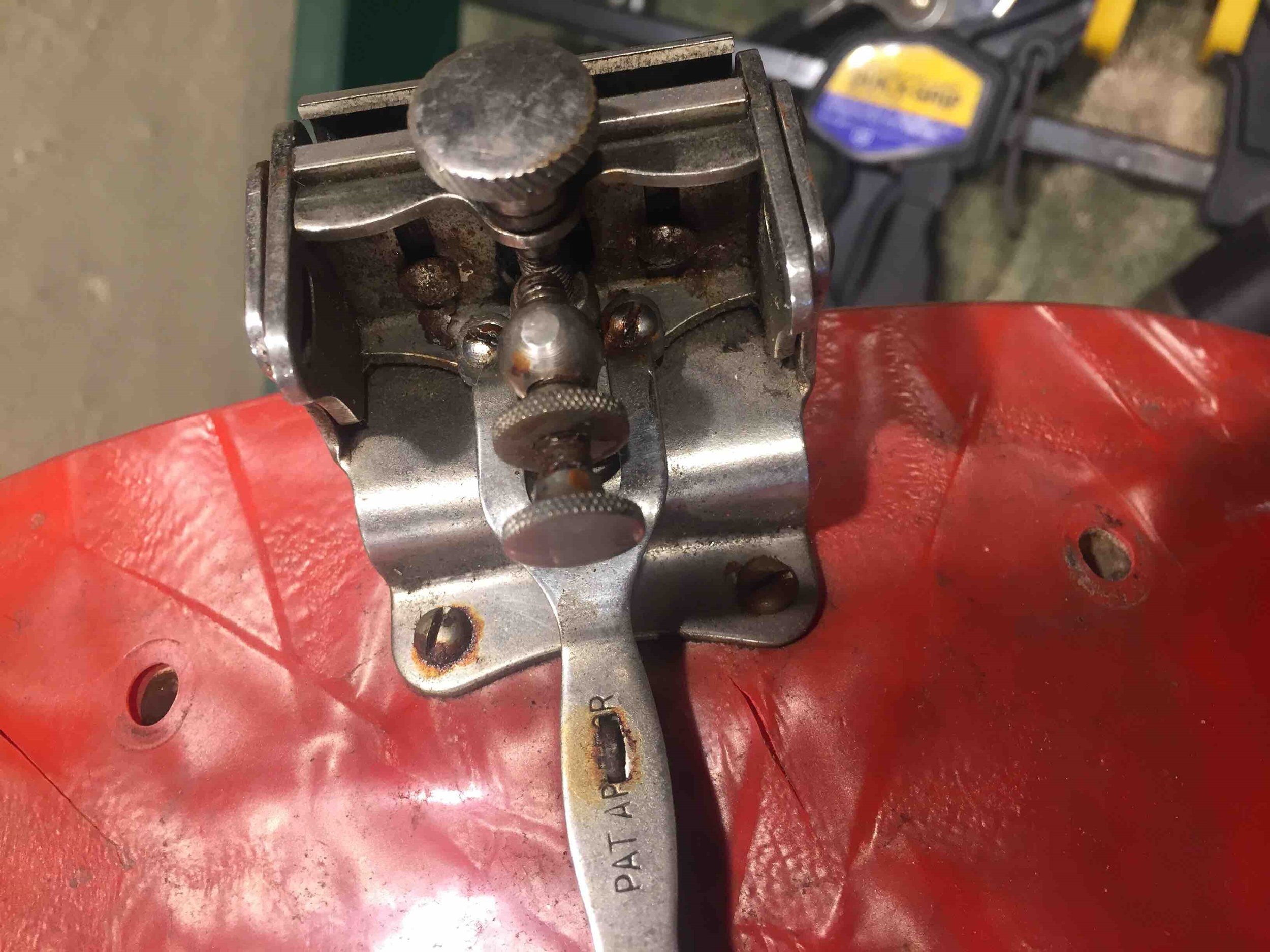
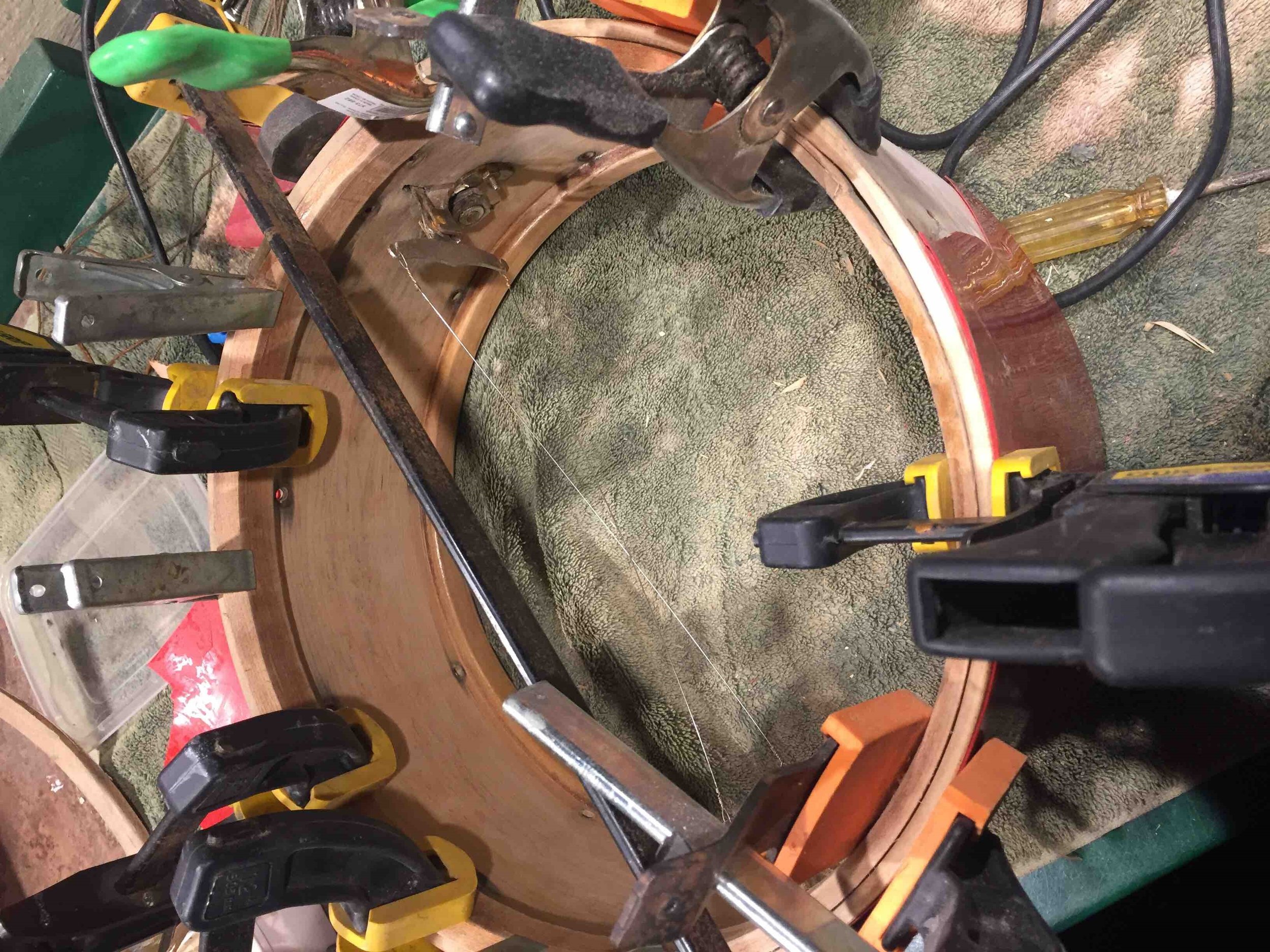
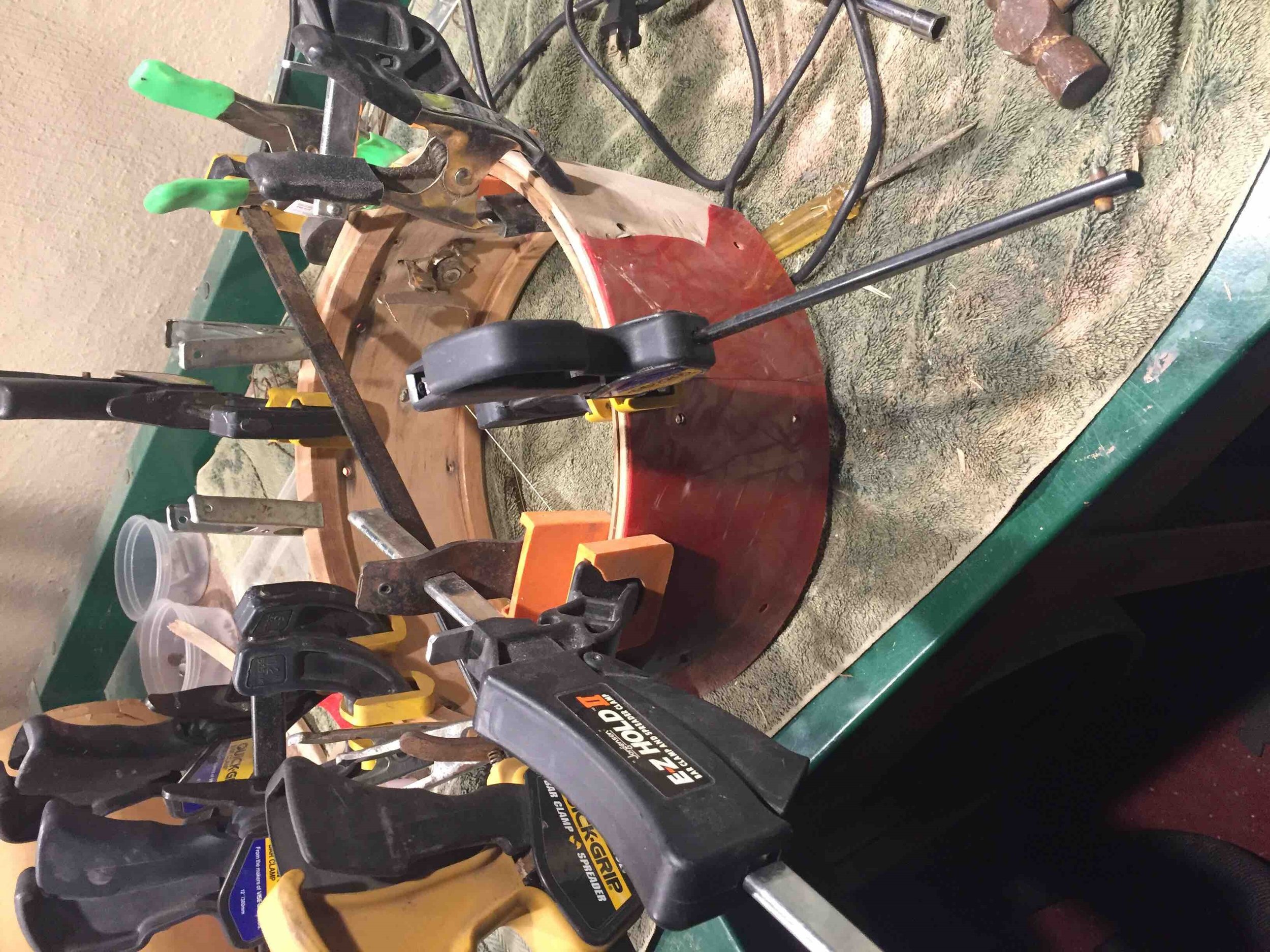
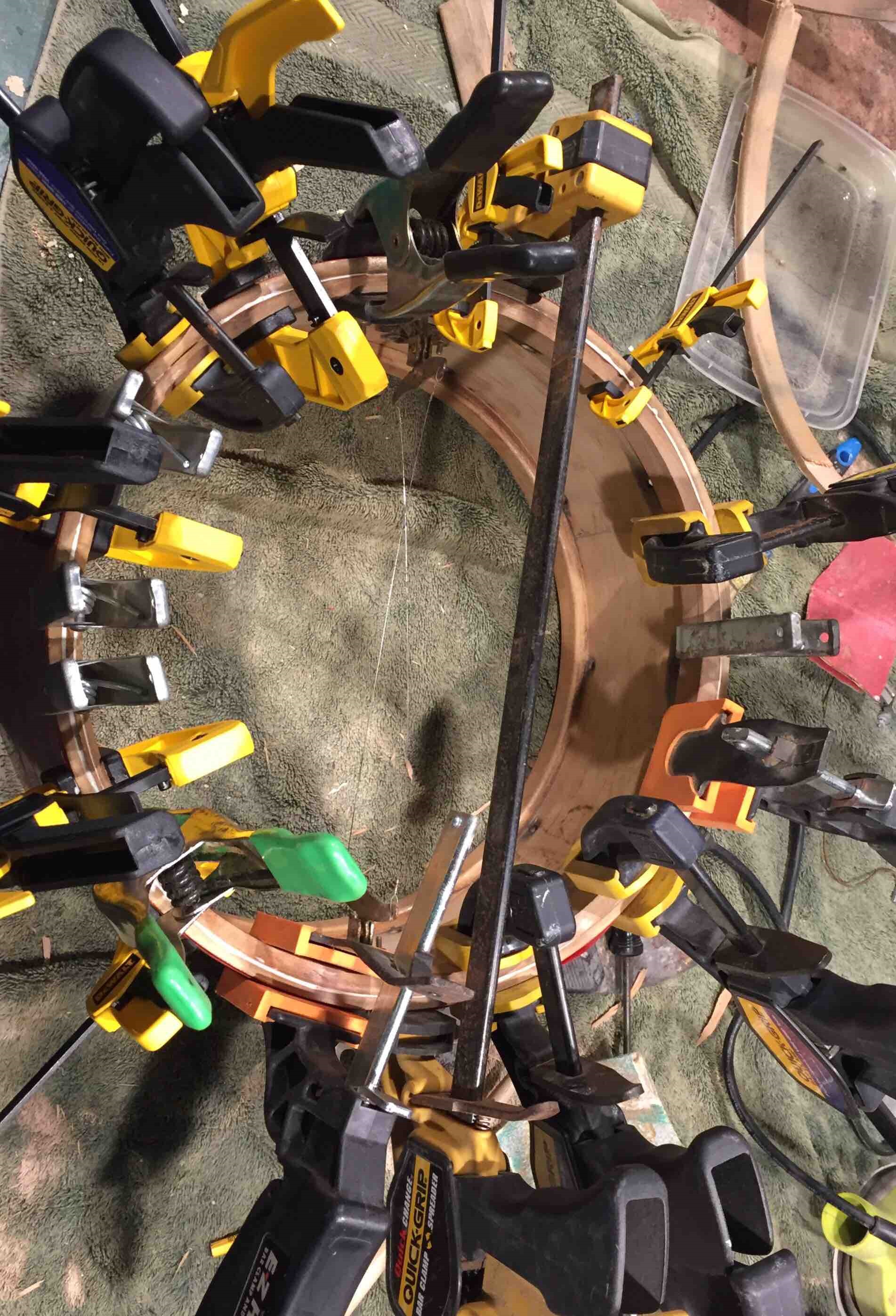

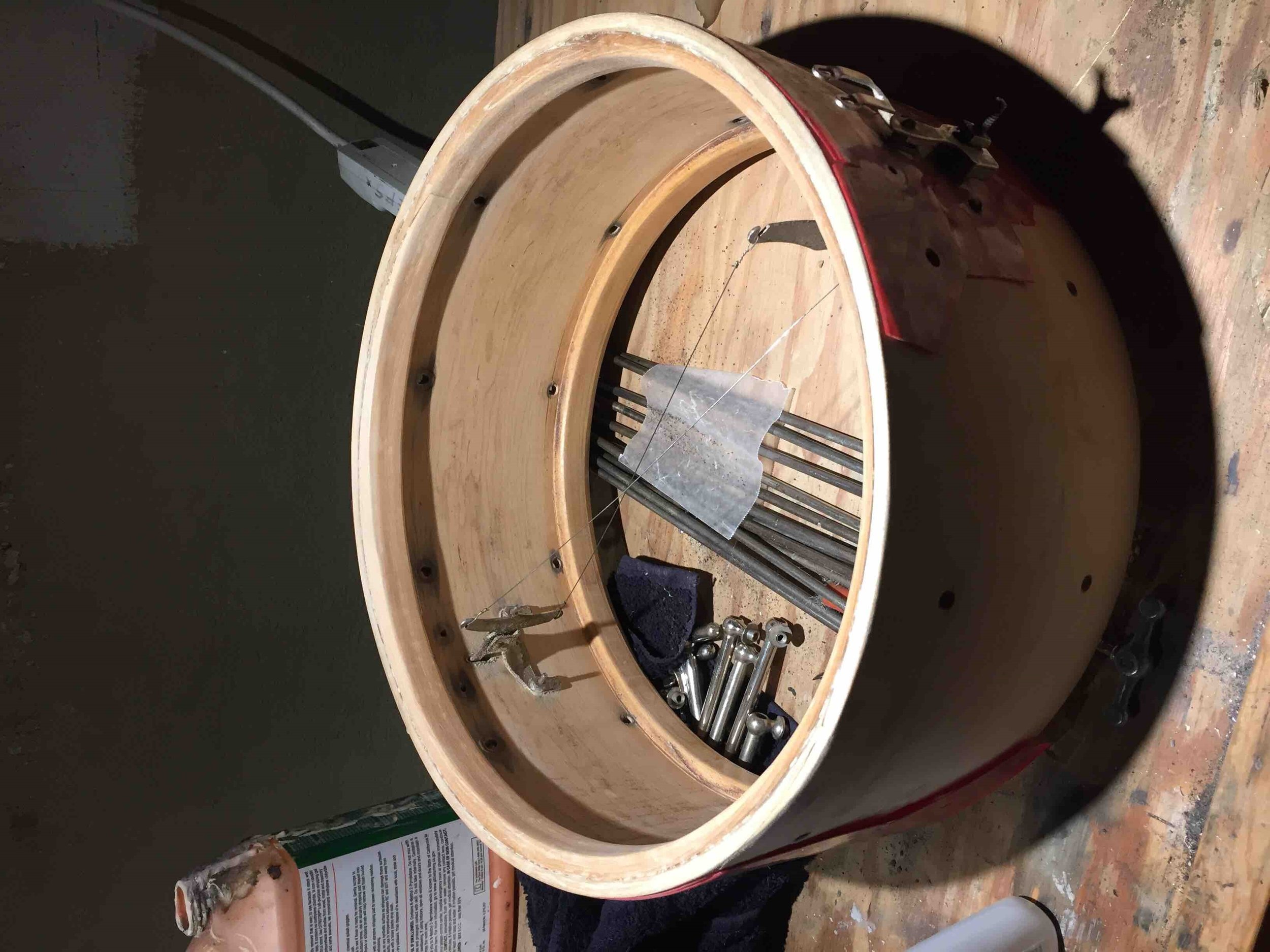
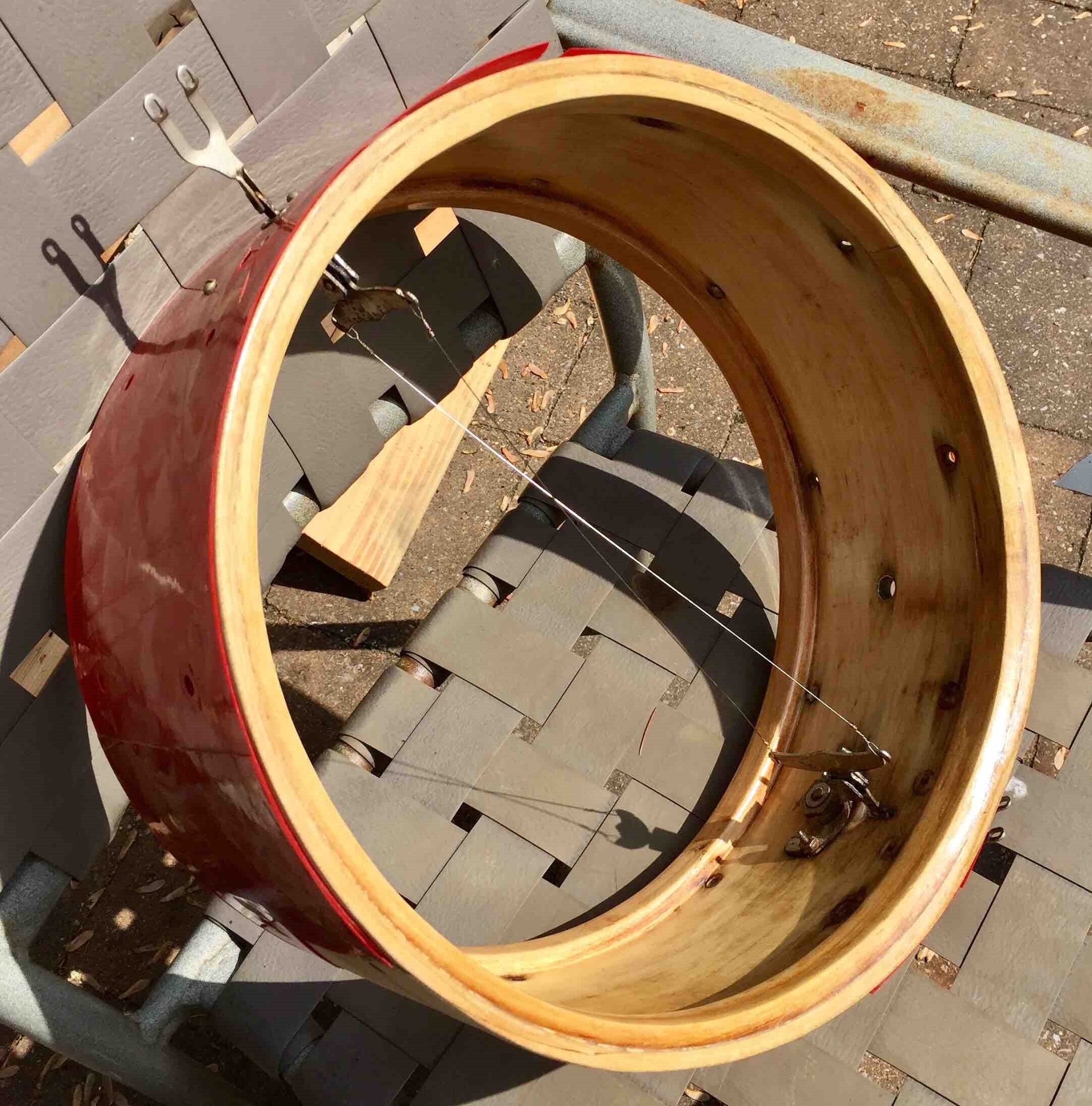

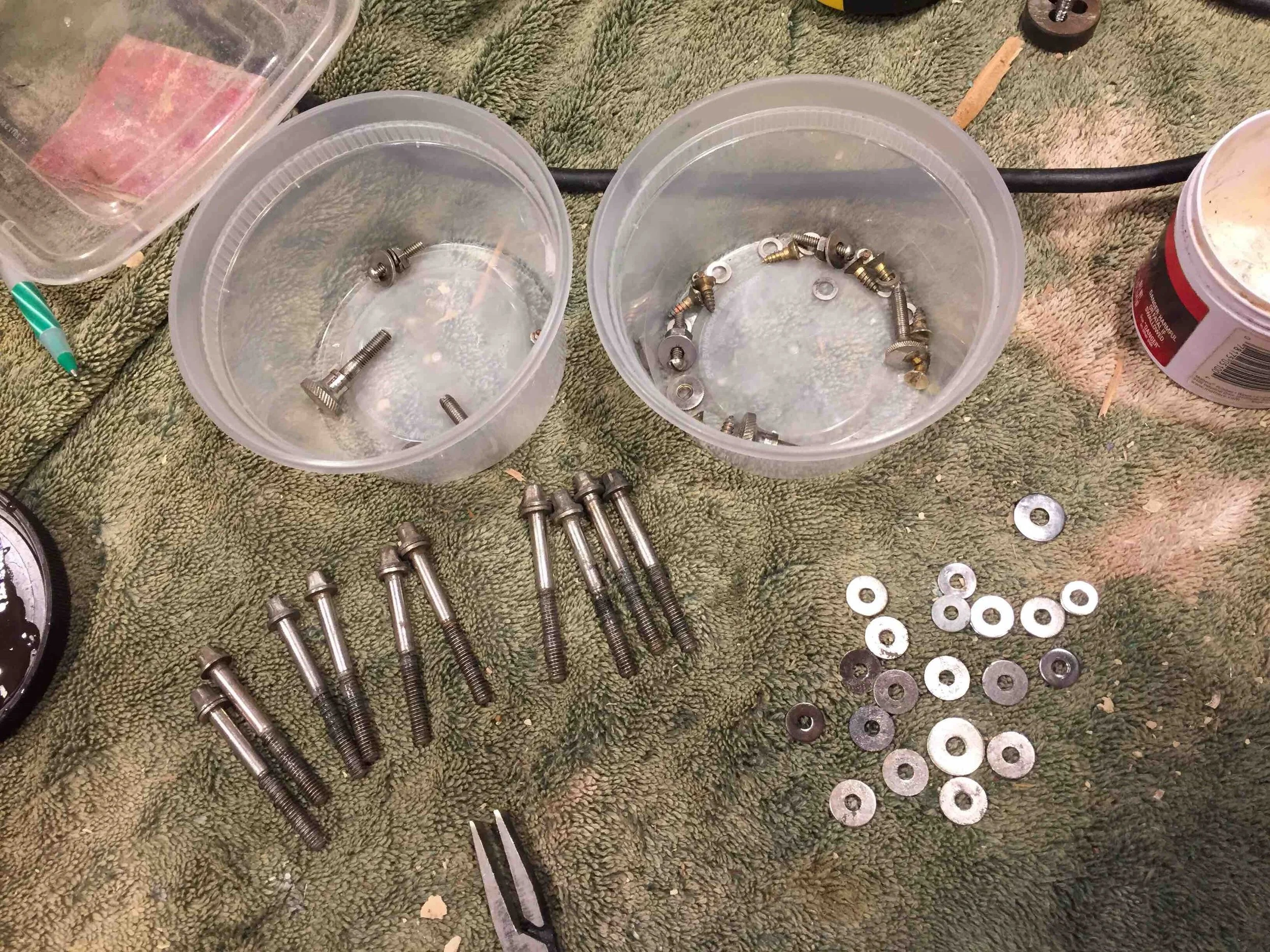
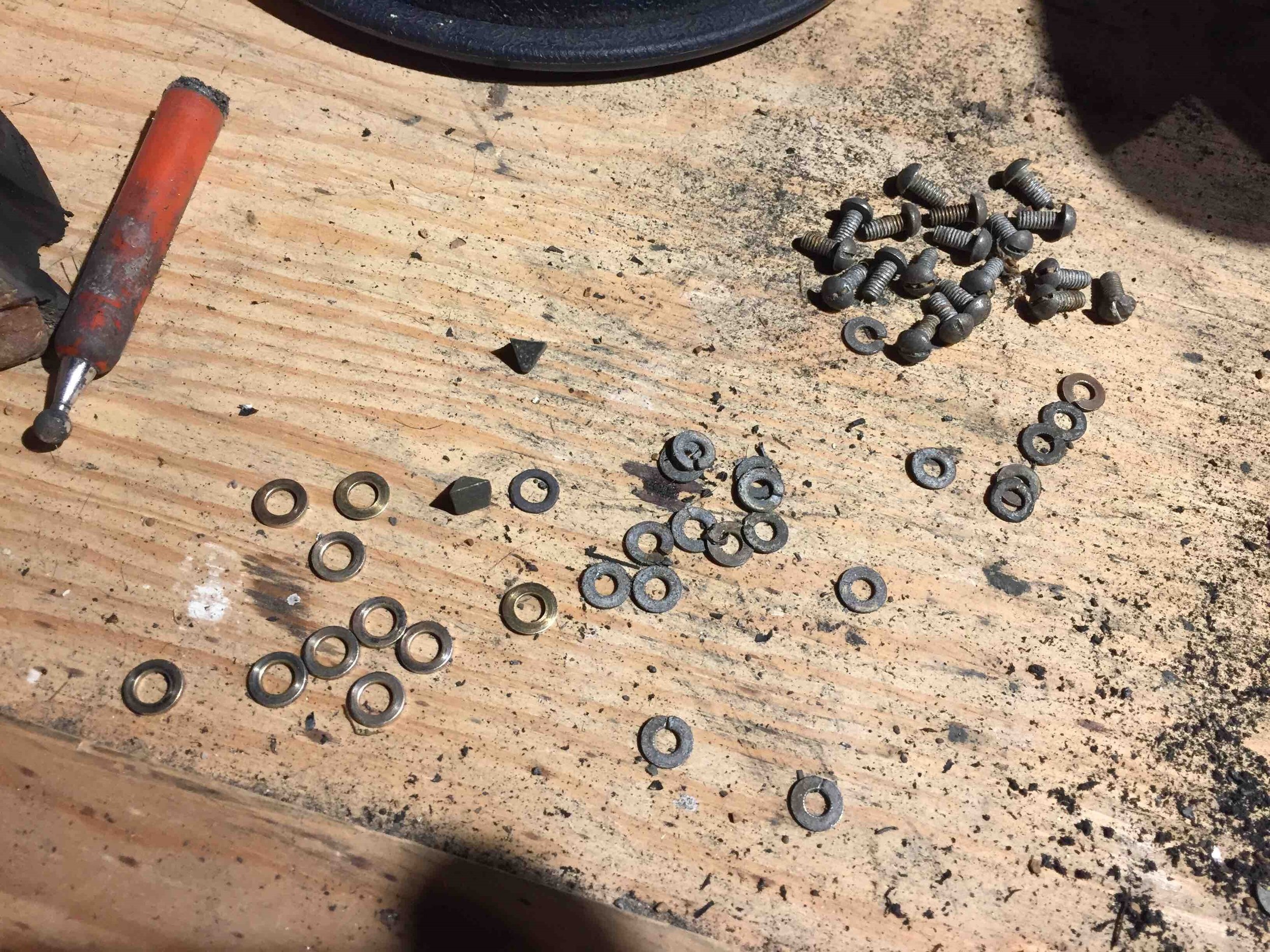
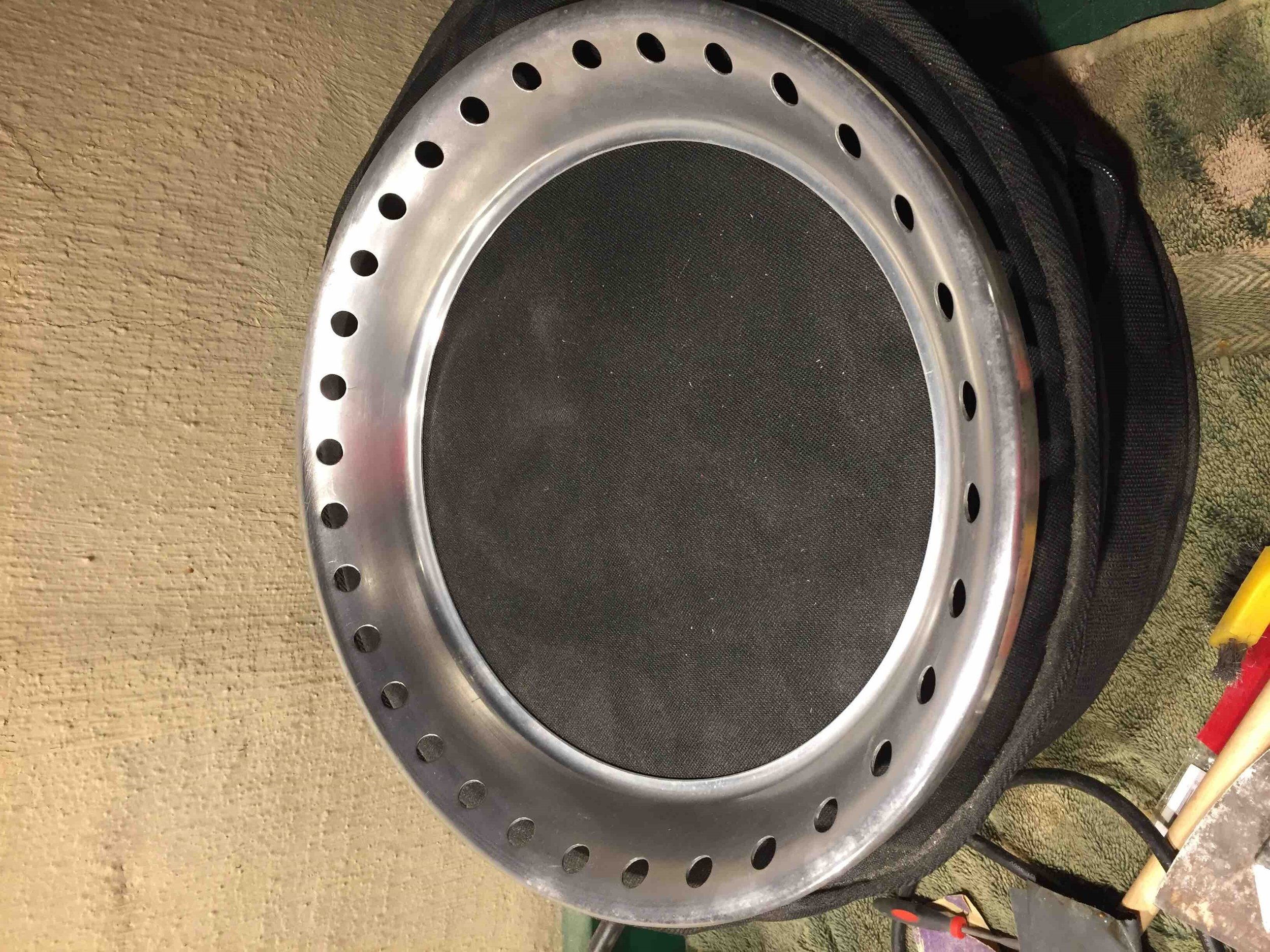
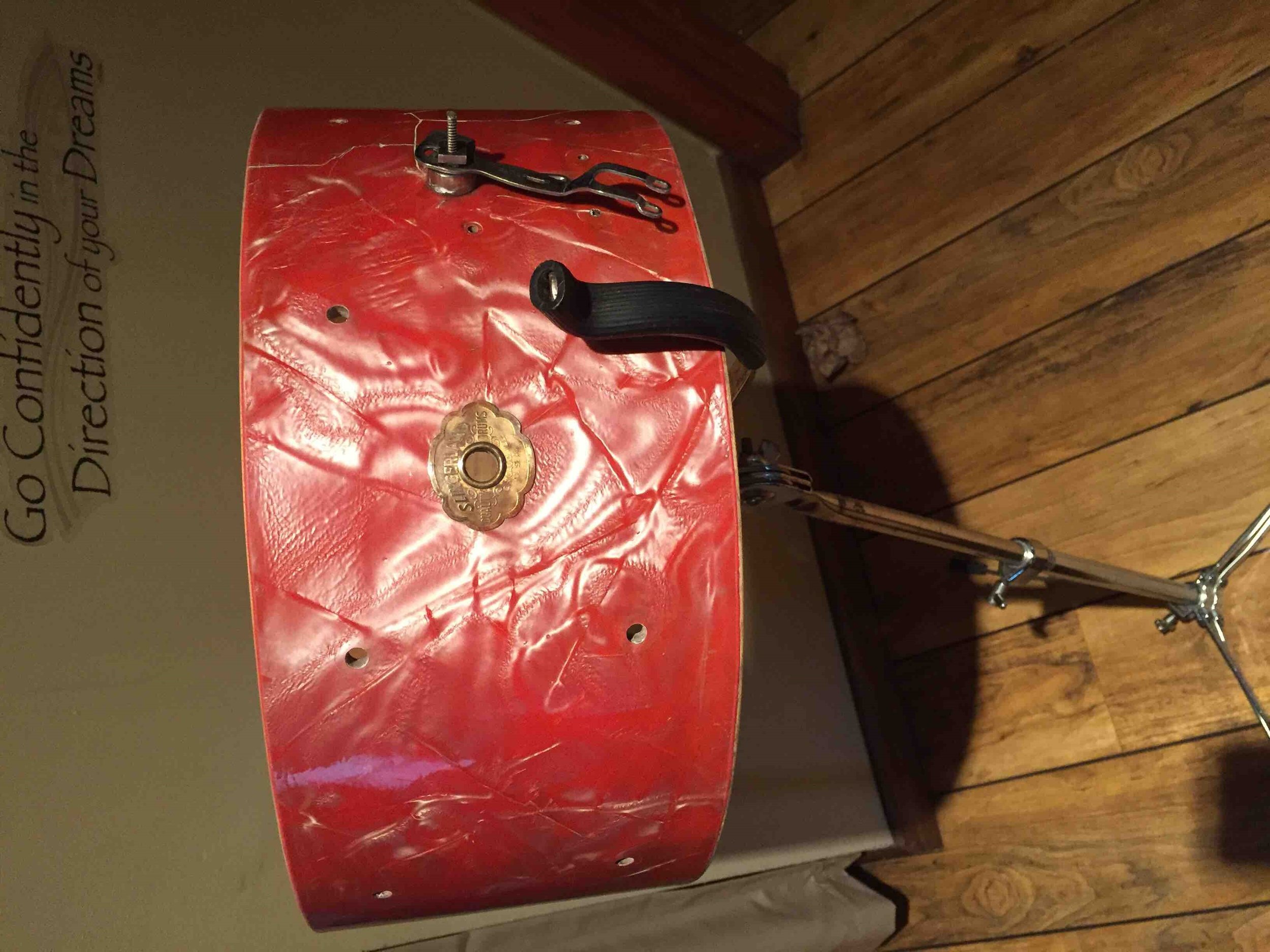
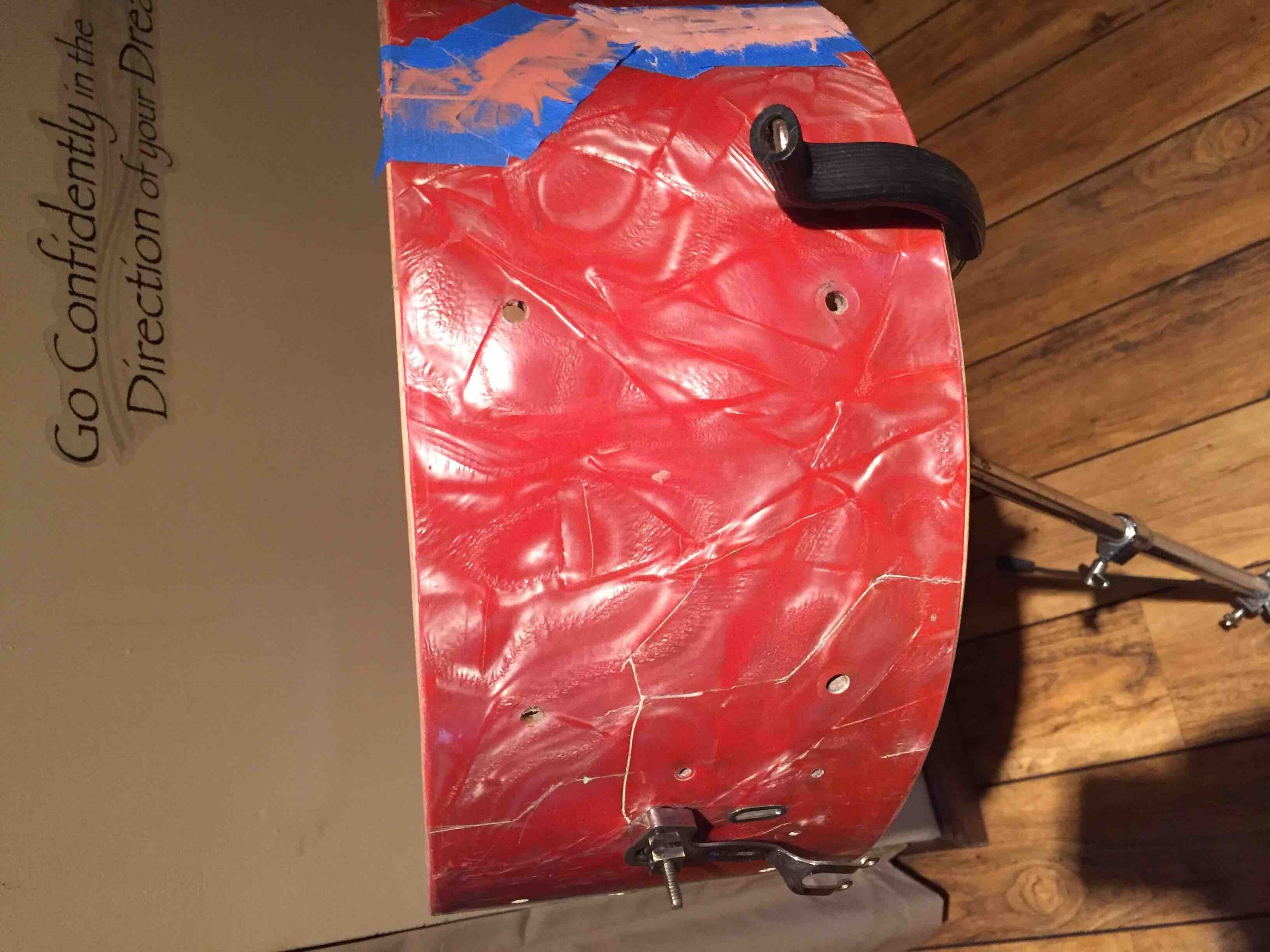
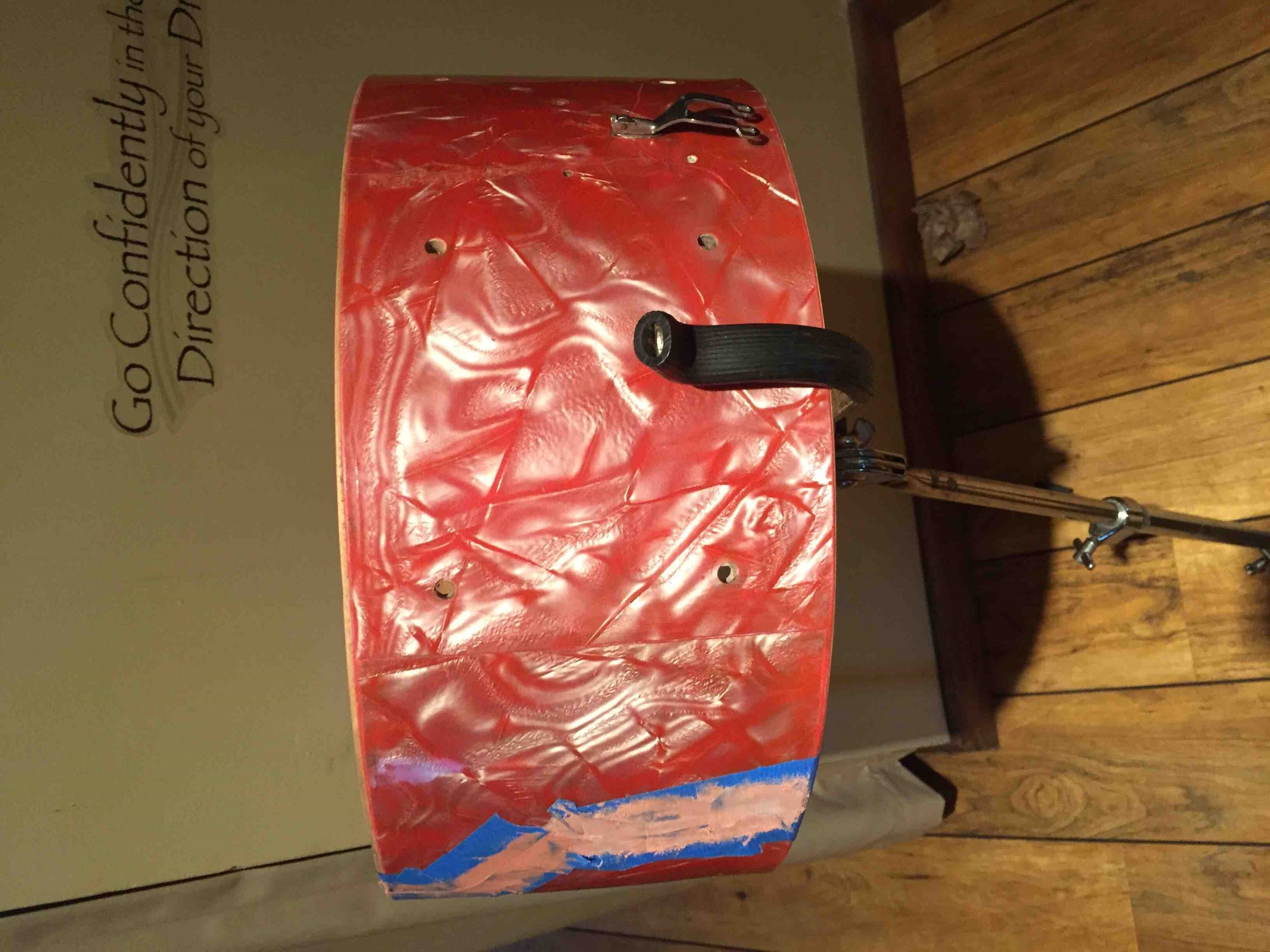
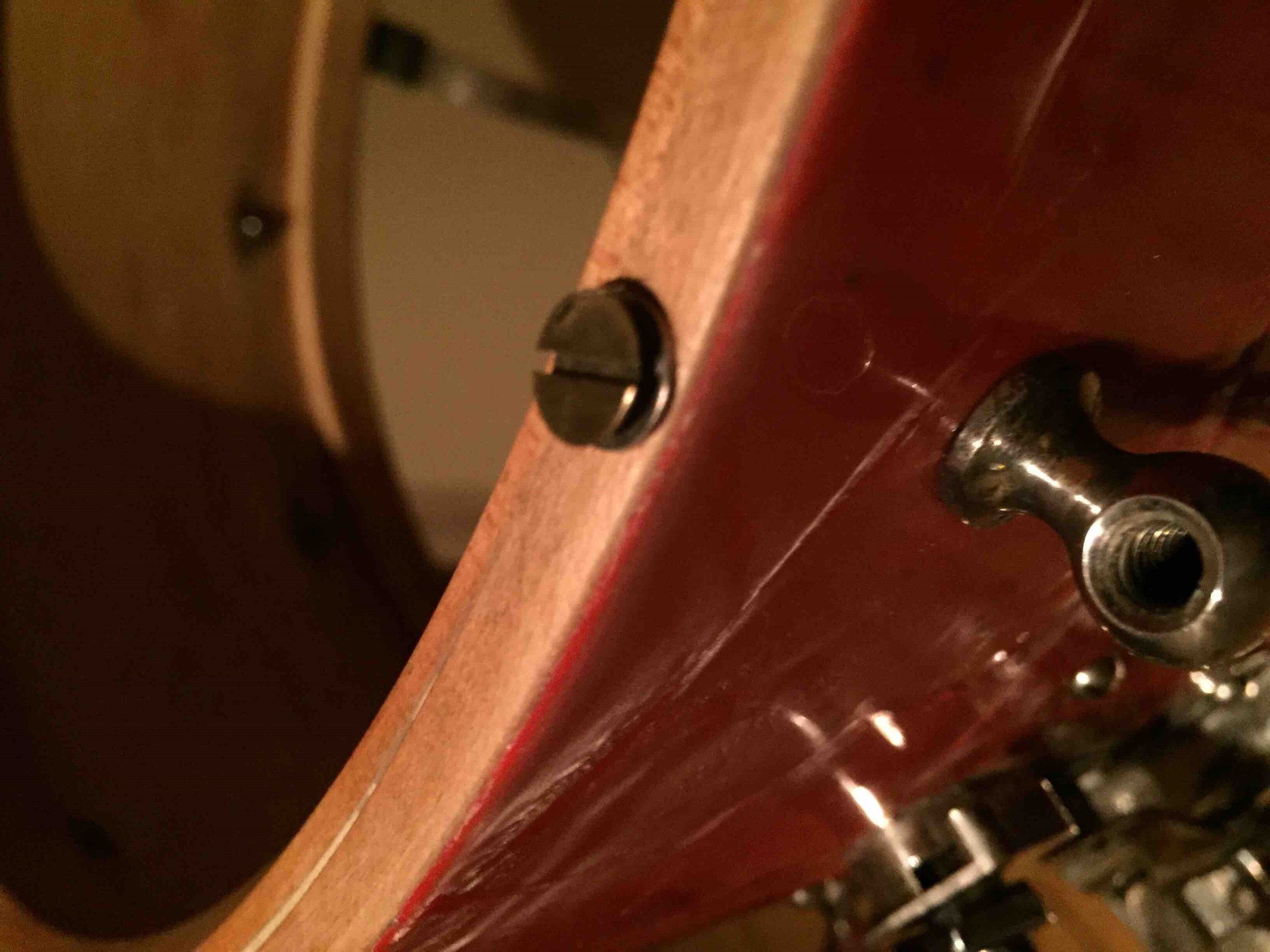
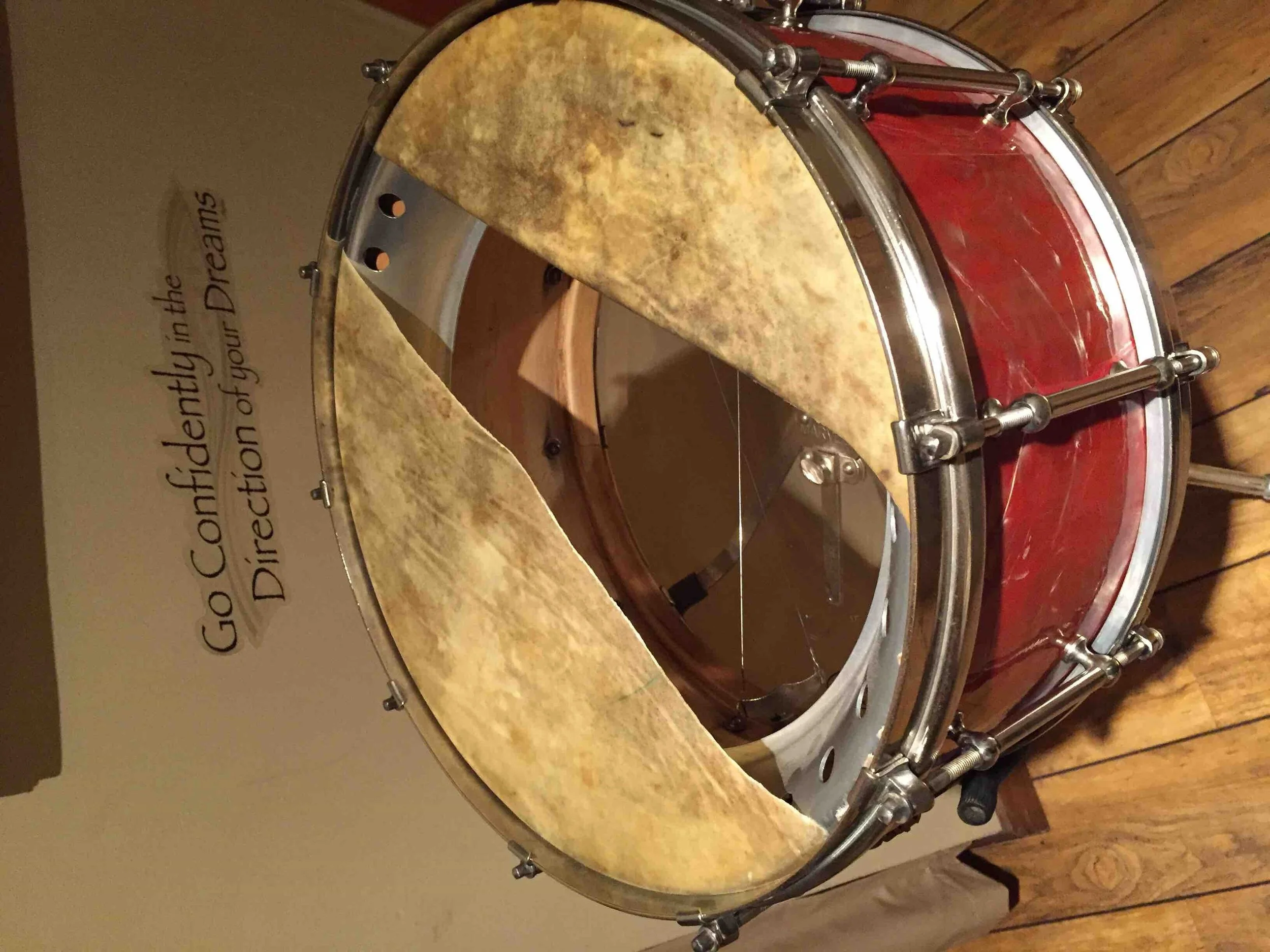
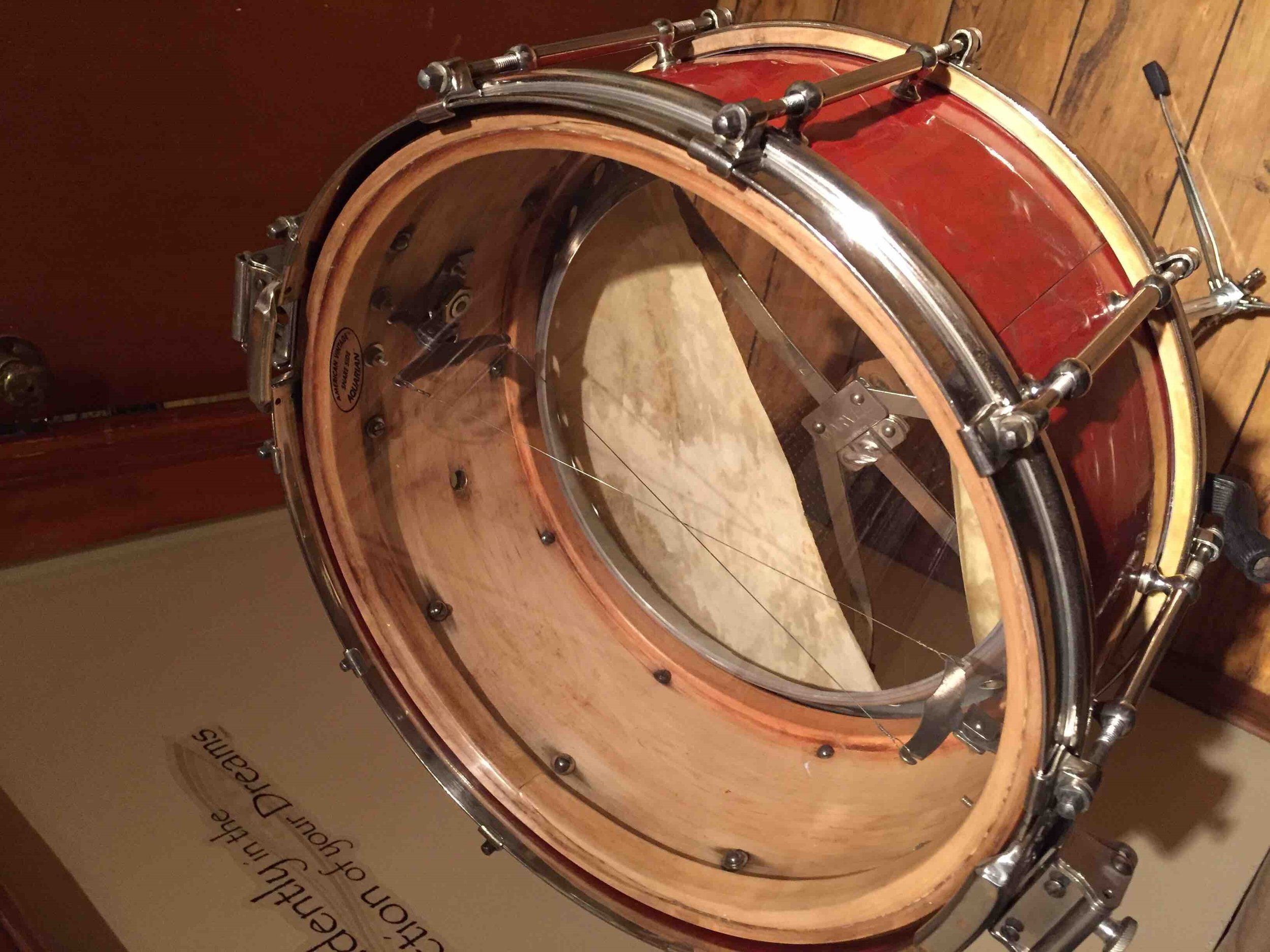
Mike Curotto -
This latest addition to the collection came from the 2019 Chicago Vintage & Custom Drum Show. The load-in is always on Friday so five minutes into the load-in I had myself a new drum, just like the old days. I had seen a few photos of the drum earlier this year and immediately thought to myself “this at best is a parts drum”. My good friend Mark Cooper walked up to me and said “did you see what Joe did with the drum?” We walked over to Joe Mekler’s (AKA Joey Boom) booth and KABLAM! This is one of, if not the most amazing restorations that I have ever seen. A lot of you fellow collectors know how excited I get when an ultra-rare snare drum comes my way but in this case I was more astonished at the restoration of this drum than I was at being able to add this drum to my collection. My words will not do this restoration as much justice as master restorer Joe Mekler’s own words so I am going to step back and present you with Joe Mekler’s amazing restoration of a 1932-34 Slingerland 6.5 x 14 *Rose Pearl Artist Model DuALL.
*Rose Pearl on any Ludwig, Leedy or in this case Slingerland is extremely rare. Rose Pearl on an Artist Model DuALL is ultra-rare. At this writing I know of only two Slingerland Rose Pearl DuALLs, the 6.5 x 14 in this article and a **5 x 14.
**The 5 x 14 is also in my collection, I’ve included a photo for historical value.
Enjoy this amazing story. Take it away, Joey Boom.
Joe Mekler -
“This drum is a prime example of ‘They are still out there’. It was located in a basement in Cape May NJ and was acquired at an estate sale of the property and contents. It was accompanied by a Rose Pearl 28” Bass Drum, some typical small accessory clamps, parts and cymbals. The Bass drum has a mahogany exterior ply on the shell and the DuAll snare is a solid maple shell. This is mentioned because the translucency of the pearl finish takes on the hue of the wood underneath of it. The rose pearl over mahogany has a burgundy hue and the same pearl over the much lighter maple displays the actual vibrant rosy pink. There were no back-stories available from the estate company or from the family selling the home contents. The drums etc. quickly changed hands after the initial estate sale purchase to the former owner and restoration specialist Joe Mekler aka ‘Joeyboom’ to its present residence in my collection. The utmost of worst environments was home to these instruments for possibly decades. A Non temperature controlled, dark, damp, wet basement. Every system and part on the drum was affected in one way or another from the neglected forgotten storage. The resonant side of the shell separated at the lap seam and became egg shaped beyond its normal 14” diameter. This was due to the reinforcement ring splitting separating and resembling the letter ‘G’. This also in turn wrinkled, curled, split and bubbled all of the Rose wrap. Most of the metal tuning and snare throw parts were rusted and frozen in place. In spite of all of this damage that required some intense major surgery, there was wonderful news. ALL OF THE NUMEROUS TINY PARTS WERE PRESENT!!! Also considering that this drum was the 2nd version of the DuAll snare mechanism utilizing the cantilever arm and crossed thin cable wire design, ALL OF THE PARTS SURVIVED!
The batter side of the drum has the aluminum tone flange and flat bearing edge with evenly spaced wood screws that a 1/8” diameter steel ring rests upon tucked up in the underside of the flange. Luckily, although badly split, the original top head and FLESH HOOP were both present. This is a vital part to the drum as the diameter of a 14” tone flange requires a flesh hoop and top head diameter approximately 14 1/8-1/4” and a taller collar on the head. The original top rim allows for the extra size needed. This allowed Ryan McKay of Bovid Percussion the ability to tuck a beautiful new skin head on the original flesh hoop for a perfect seating. The repairs and restorations required returning this special gem to as close to its factory original condition were as follows. [see pix above]
1. Typical Dawn soak/vibratory tumbler/buffing wheel/hand polish/wax of almost every single metal part. The tiniest parts were hand cleaned/polished.
2. One side of the throw mechanism pass through arm was riveted on both sides of the shell and could not be removed. Therefore it became a restoration obstacle.
3. A major portion of the wrap had to be cut away following the pearl striations of the pattern.
4. The shell had to be clamped to 13 7/8”, glued and clamped to join the separated seam and have the shell expand back to 14” round diameter.
5. The reinforcement ring was so badly damaged that it had to be carefully spray soaked with water and vinegar and removed from the shell. A 30s Radio King donor shell was pan soaked to reactivate the hide glue and both rings were carefully removed from it. The snare beds of the donor drum were too deep so the batter ring was soaked again to separate it from itself at the scarf joint. It was then immediately clamped into its new home as the diameter was ever so slightly different. After complete drying, it retained its roundness but however had to be sculpted and reshaped so the diminishing scarf joint would lay as flat as possible and retain a perfect circular interior shape and look as original as possible. It was then removed glued fitted back in, seated and clamped. It was then bleached to match the rest of the drum. The shallow beds were then hand sculpted to match the shell bed depth and taper. The entire ring was then sculpted to match the bearing edge and not impede at all upon their original shape and taper.
6. There was a bit of a bulge in the shell that had to be carefully sanded back down to round so there would be a maximum refit for the wrap.
7. The wrap had to be fit back together in several places with crack edges Dremel sanded and shaped to allow no overlap for complete level flatness as some of it was still glued to the shell and much of it was a scission. Pieces of the badly knurled wrap had to be taped to another shell and heat treated to relax and reform to flat slightly bowed normalcy. Two types of glue were used to accomplish this goal. Contact cement was used on the existing connected parts and ALL of the cracks and lifted splits. A glue syringe was used to inject the cracks and in many cases heated treated and clamped the next day to guarantee full adhesion. The largest piece was joined with wood glue. This allowed for shifted placement before adhesion of the piece to gain absolute edge tightness and closeness on a very exposed panel. This left an unavoidable ¼” opening between the wrap round the back of the drum. The shell below it was deepened a bit to a valley and Bondo auto filler was used to fill the crack. Wood filler was used on all of the other cracks and splits and then everything was color match painted. 800-2500 sand paper was used followed by various grades of liquid cut and polish to wax to achieve a vintage sheen of the original plastic surface to match completely around the shell. No top coat spray was used. 3 tube lug holes had to be reshaped to allow for proper assembly.
8. All cleaned, rust removed, polished metal bits were then reassembled and lubricated with a final fingerprint and dust abatement of the entire drum.
9. The tone flange was completely cleaned buffed and polished and seated over the wood screws. The new calf head was fitted to the top and a clear plastic head on the bottom to expose Slingerlands attempt to dodge the patent infringement of the unique throw system. This was a remarkable find and a perfect progression of ownership that lead to a restorative resurrection of a very special, at this point, ‘one of one’ historical instrument.
Joe Mekler aka “Joey Boom”